Top 7 benefits of gasketed plate heat exchangers in industrial processes
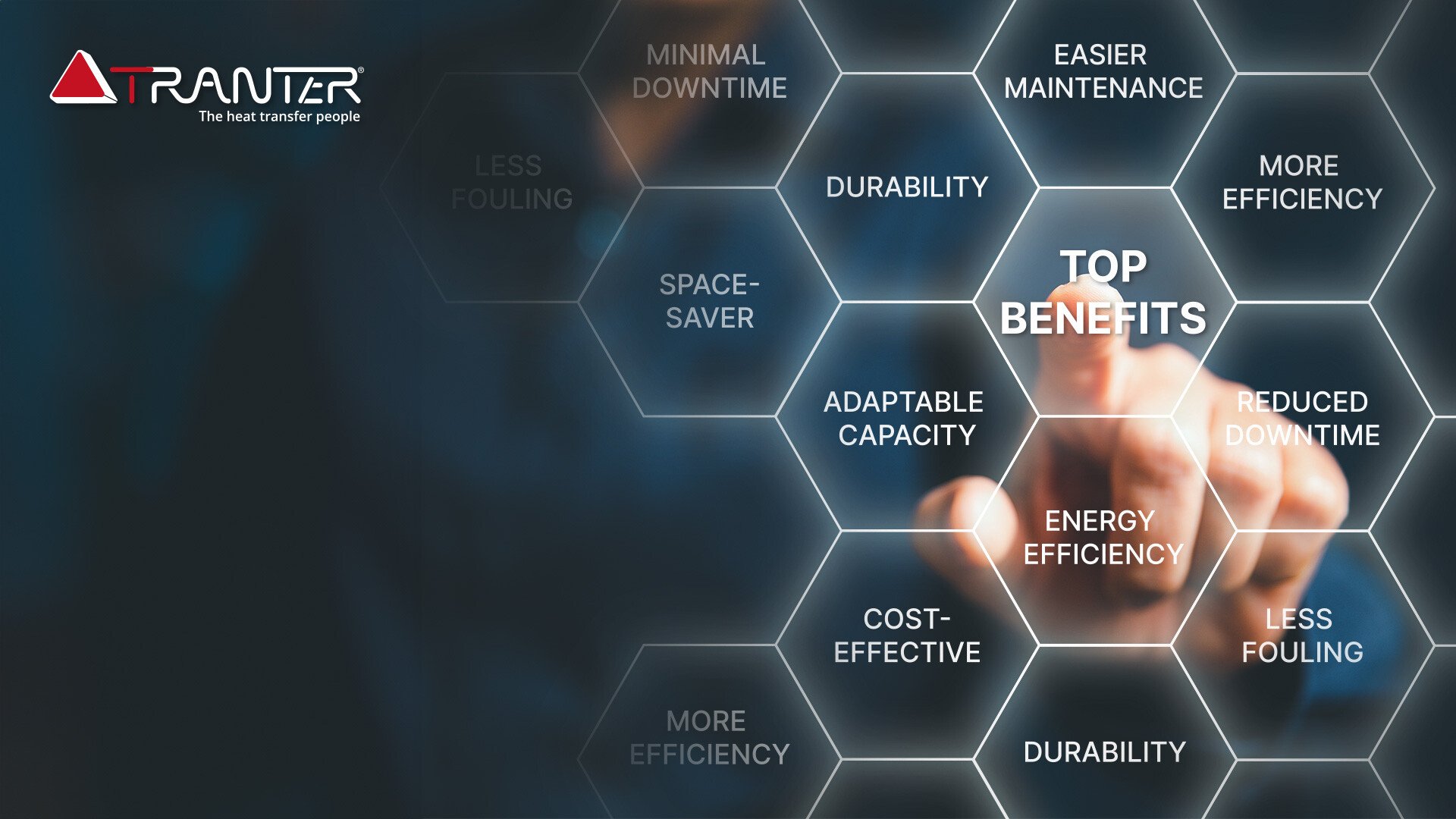
In your role, you're always looking for ways to boost the efficiency and cut costs of your operations. Gasketed plate heat exchangers (GPHEs) are a big part of that strategy. They're versatile, working across various industries like chemical, petrochemical, power generation, and marine, to precisely manage temperatures – whether cooling water or processing fluids in your plant or heating it.
They're compact, energy-efficient, and easier to maintain than traditional exchangers. Plus, their design minimizes your environmental impact with more obtainable heat recovery. With GPHEs, you're not just keeping operations smooth; you're optimizing for the future, ensuring your processes are sustainable and cost-effective.
1. Easier maintenance for minimal downtime
Imagine servicing and cleaning a gasketed plate heat exchanger instead of, say, the traditional shell and tube types. Gasketed plate heat exchangers are a breeze to handle in comparison. You can simply open them, clean them up, and put them back together without a huge fuss.
This means less time messing around with maintenance and more time keeping your processes up and running smoothly. It's a practical, no-nonsense choice that ensures you're not bogged down with unnecessary downtime.
2. More efficiency, less space
Gasketed plate heat exchangers are real game-changers thanks to their reliability and top-notch heat transfer efficiency. Think of them as the dependable workhorses of your operation, consistently performing under various conditions and ensuring the uptime of your processes.
What's more, their efficiency is a space-saver. You get the same (or better) heat transfer capacity but in a smaller footprint, which is perfect for tight spaces. This means you can optimize your plant setup without compromising on performance, making every square inch of your operation count.
3. Designed for durability
With GPHEs, safety and reliability aren't add-ons – they’re part of the core design. This makes your operations not only efficient but also safer and more dependable.
Made to withstand harsh conditions, GPHEs ensure minimal leaks and operational failures. Adding to their appeal, these heat exchangers are renowned for their robust construction and ability to maintain performance over time, underlining reliability in every aspect.
4. Adaptable capacity for dynamic demands
Gasketed plate heat exchangers’ modular design is a standout feature. Want to ramp up capacity? Just add more plates. Need to dial it back? Remove a few.
You just don't get this level of flexibility with traditional shell and tube exchangers, making GPHEs a smart choice for industrial environments where demands can shift.
5. Unmatched energy efficiency
GPHEs offer a solution that benefits both the environment and the bottom line by optimizing heat transfer and reducing the energy input needed for the process.
In other words, thanks to their clever design and operation, you're looking at lower heat loss, which translates directly into energy savings.
6. The friendliest option for your wallet
Regarding costs, gasketed plate heat exchangers often edge out their shell and tube counterparts – especially in the long run. The choice of materials for your heat exchanger plays a significant role in this equation. Depending on the specifics of your process and the fluids involved, the required materials can vary widely.
If expensive, exotic materials are needed, opting for a GPHE means less of those materials compared to large shell and tube systems. Combined with the compact, space-efficient design of gasketed plate heat exchangers, this translates to lower installation and operational costs – offering a smart, cost-effective solution for your process.
7. Less fouling = lower total cost of ownership
You'll notice far less fouling with plate heat exchangers than you would with the shell and tube types. Why? It's all in the design. These exchangers keep the flow turbulent, even at low Reynolds numbers, and apply just the right amount of stress to keep buildup at bay.
Less fouling means you're not constantly pausing for clean-ups, reducing both your downtime, maintenance costs and overall TCO. GPHEs offer a smoother, smarter way to manage heat exchange that keeps your operations lean and efficient.
The path to optimizing your industrial cooling and heating processes doesn't end here. The next step? Learning how to balance budget and performance in heat exchanger selection. This essential read will guide you through the decision-making process, ensuring you hit the sweet spot between investment and operational excellence.