How to balance budget and performance in heat exchanger selection
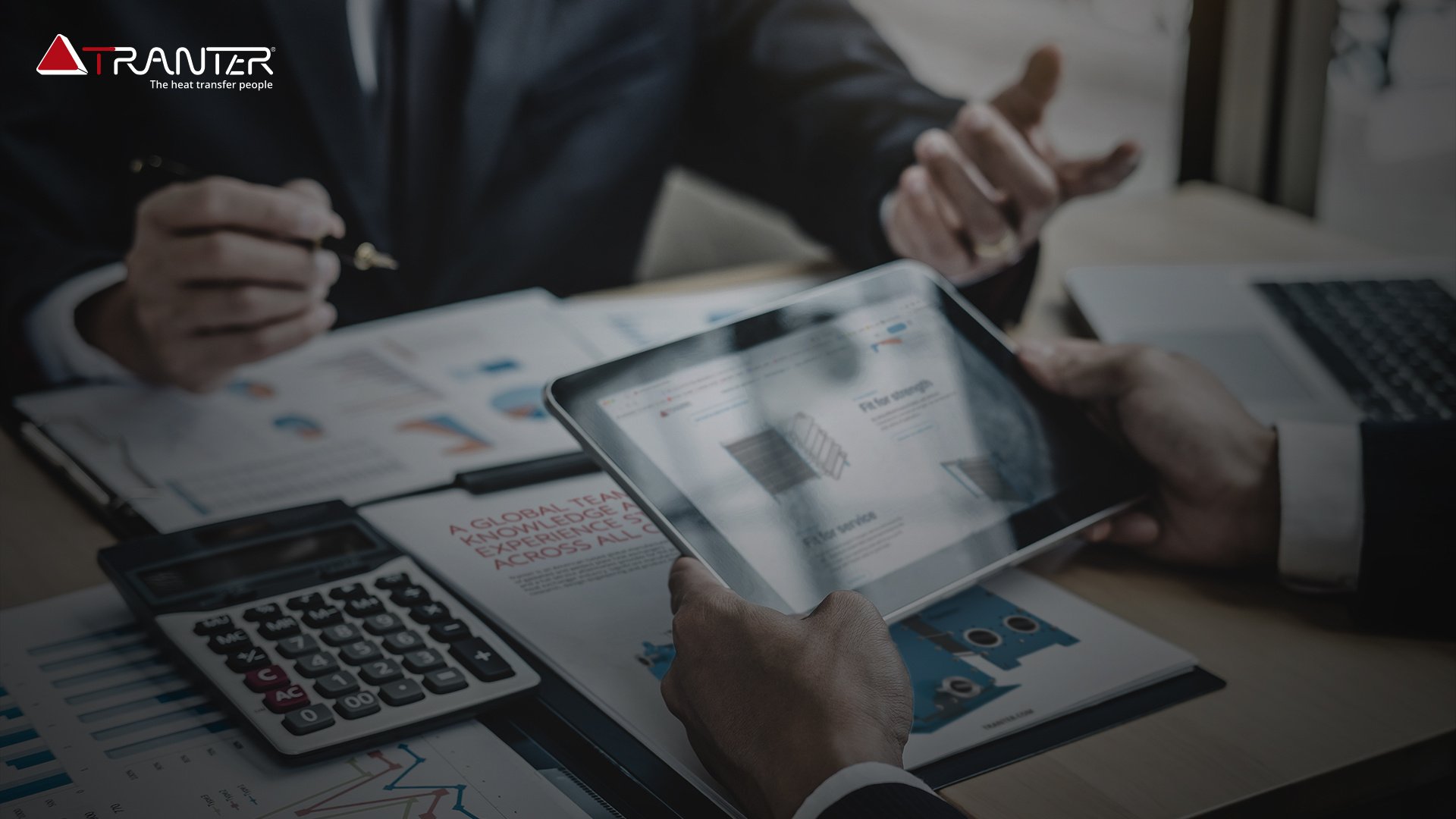
1. Ensure harmony between pump size and efficiency
Facing the reality of balancing pump size and heat exchanger efficiency brings its own set of challenges. As a Process Engineer, you've heard it before: dealing with hefty pressure drops means sizing up on pumps. But that's not just about bigger hardware – it's a budget and space puzzle, too.
The best move here is to dial into the perfect sync between your pump and heat exchanger. And you can’t just think about making do; you have to make smart choices. Talk to your supplier
about cutting-edge options that keep your setup lean and mean without compromising on performance. Finding that sweet spot where both the pump and heat exchanger are in harmony can turn a challenge into a highlight.
2. Consider how often you need to service your heat exchanger
Imagine this scenario: It's that time of the year when maintenance on your heat exchanger is due. Now, what if this year, instead of the usual multiple shutdowns, you only had to halt production once or twice? Not only does this mean less downtime and hassle, but it also frees up a chunk of your budget. Suddenly, you're not saving costs; you're investing in performance.
In other words, by selecting a heat exchanger designed for low maintenance (while still considering your specific process), you're making a smart move. Less maintenance means lower costs, which, in turn, means you can channel those savings into boosting the efficiency or reliability of your process. It's about making every dollar work harder for you, ensuring that your heat exchanger both meets and exceeds expectations – all while keeping a tight rein on costs.
3. Opt for connections that meet your process’s standards
Here's another scenario: you're eyeing studded or standoff connections, thinking they might offer an edge. But pause for a moment and consider this: are they truly adding value, or just extra cost? While these “nice-to-have” features might seem preferable, they can bump up costs through additional materials, welding, and the space they occupy (not to mention making the unit heavier).
Shift focus to balancing the pressure drop effectively. It's about weighing the real benefits against the added costs. By opting for standard connections that meet your process’s requirements without overcomplicating the design, you can maintain efficiency and manage costs better. To be sure you do it right, engage with your supplier about the specifics of your application to find a solution that balances performance needs with budgetary constraints.
4. Don’t pick the “best” materials
There's a common misconception that only the "best" will do when selecting materials for heat exchangers. Some argue for high-end materials, believing they offer unmatched durability and performance. However, this overlooks a crucial aspect: suitability is king. By simply picking the best materials out there, you’re not considering the unique demands of your process fluids and operational environment.
Instead, go for materials that perfectly match your specific needs. This strategy ensures your heat exchanger's longevity and avoids unnecessary expenses on over-spec materials. Identifying materials that withstand your process conditions without breaking the bank is a wise move (your supplier could help with this, too). This approach guarantees performance and durability, tailored to your requirements, ensuring a smart investment in your heat exchanger’s future.
5. Remember that size matters
When you're handed a list of requirements with those daunting maximums, minimums, and safety factors, it's easy to fall into the trap of oversizing your heat exchanger. While seemingly cautious, this approach can lead to unnecessary costs and a bulkier unit than you need.
Here's the deal: Dive into understanding the normal operational range of your unit. Tailor your safety margins smartly – think optimizing the surface area for fouling rather than just bulking up the size. This way, you're not just preparing for the worst-case scenario but optimizing for everyday efficiency. And, by evaluating how the unit performs under various conditions, you ensure that you're investing in versatility without overcomplicating or overspending.
6. Find the right supplier
As a Process Engineer, you're juggling complex designs and specifications against the hard numbers of a budget. The tricky part is finding a supplier who goes beyond the necessary – ready to roll up their sleeves and dive into the trenches with you, and find that sweet spot between the two.
The solution? Initiate conversations early with suppliers who show they're more than just vendors – they're collaborators. In other words, those willing to understand the unique aspects of your project and offer flexible, innovative solutions that will both meet your needs and exceed them, all while keeping your budget in check. This approach balances cost and performance without cutting corners on quality or efficiency.
7. Tap into your supplier’s expertise
Juggling maintenance and operational costs is like trying to keep all your plates spinning without letting any fall. When you're faced with equipment prone to heavy fouling, which could clog up several times a year, the decision-making process becomes even trickier. You might find yourself leaning towards solutions that incur higher operational costs upfront to reduce maintenance down the line.
This is where tapping into your supplier’s expertise becomes invaluable. They're your go-to for balancing budget and performance when choosing a heat exchanger. Engage candidly with your supplier, leaning on their hands-on experience to guide you. The blend of technical considerations and expert advice ensures you're making informed decisions that fit your budget and enhance your process’s efficiency and durability.
Some final advice
A solid understanding of heat exchanger technology is key to optimizing performance and cost efficiency. Here's a nugget of wisdom from Tranter expert Simon Gittins, that embodies this perfectly:
“You have to both navigate through initial costs and consider the entire lifespan of the unit. Engage in thorough discussions with suppliers. Remember, the right one is there to assist, not to sell. Through this shared dialogue, we can craft the best solution, ensuring the heat exchanger not only fits your current needs but also supports your process over its lifetime."
— Simon Gittins, Area Sales Manager
Now you’re an expert at balancing budget and performance in your heat exchanger selection. But the insights shared here are just the beginning – optimal decision-making is still one read away. To further ensure your next heat exchanger perfectly aligns with the needs of your process, you need to know exactly what to check before saying yes to a heat exchanger. Curious? Download the checklist today!