Engineering hours
Maximize the benefit of our engineering expertise by utilizing our services as extensively as possible. Our team is dedicated to providing top-tier solutions tailored to meet your unique project requirements.
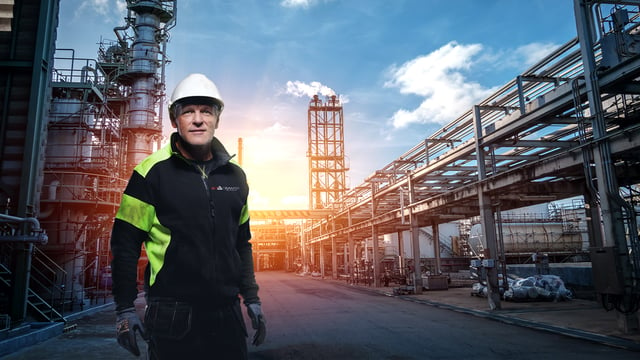
Steel production
The process of creating alumina, stainless steel, and carbon steel in the steel production industry relies on the transformation of raw materials like iron ore, coal, and limestone. This transformation occurs through critical procedures such as smelting and refining. Within this intricate process, heat exchangers emerge as pivotal components at numerous phases of steel manufacturing. Their role? To markedly diminish the use of energy, amplify the recovery of waste heat, and drive the sector towards greater sustainability.
Steel production
Maximize the benefit of our engineering expertise by utilizing our services as extensively as possible. Our team is dedicated to providing top-tier solutions tailored to meet your unique project requirements.
We know how to navigate the challenging terrain of embracing new, yet possibly untested, technologies while ensuring processes remain dependable and steady.
Gain immediate, expert advice on streamlining projects to drastically cut down on administration time. Tranter combines small-company agility and customer focus, ensuring personalized attention to every customer needs.
Steel Production
Exploring the steel production industry and the use of heat exchangers
The process of extracting aluminum requires energy-intensive procedures, including digestion, evaporation, and heating of the liquor. Manufacturers require a thorough know-how process that ensures highly reliable equipment involving heat exchangers to optimize performance, decrease downtime and increase profitability.
Sustainable or low-carbon steel employs eco-friendly production methods, such as direct reduced iron (DRI) to reduce carbon emissions, unlike the traditional, energy-intensive blast furnace-basic oxygen furnace (BF-BOF) method, which heavily depends on coking coal and significantly increases CO2 emissions. Tranter’s plate heat exchangers play an essential part in reducing CO2 emissions from steel plants through post combustion carbon capture and to recover the waste heat from the steel production process.
Heat exchangers are utilized in electric arc furnaces (EAFs) and basic oxygen furnaces (BOFs), which are common methods for smelting and refining stainless steel scrap or raw materials such as iron ore, nickel, and chromium.
Steel production is crucial, transforming iron and carbon into steel with traces of manganese, chromium, nickel, and vanadium, all facilitated by heat exchangers.
Blast furnaces typically use regenerative stoves to preheat the blast air before it enters the furnace. Heat exchangers within these regenerative systems recover waste heat from the hot off-gases leaving the furnace and transfer it to incoming cold air, improving energy efficiency and reducing fuel consumption.
To reach the NetZero goals, refineries are looking to reduce the CO2 emissions. Post combustion CO2 capture to refineries involves removing CO2 from gas streams using continuous absorption with regenerable solvents, crucial for reducing greenhouse gas emissions and fighting climate change. Tranter leads in providing heat exchangers for carbon capture, ensuring your plant operates safely and reliably.
Resource center
Energy, heating and cooling Sustainability
The digitalization mega trend has resulted in exponential growth of data centers. Let’s take a look at how Tranter’s plate and frame heat exchangers can be used to make the datacenters more sustainable.
Energy, Process industries Sustainability
Tranter’s heat exchangers have various applications across many different markets. Let’s take a look at how plate and frame heat exchangers can be used in CO2 capture applications to improve the total economy of the plant.
Energy, Process industries
Tranter’s compact plate heat exchangers are used in various energy intense industrial applications. Let’s take a look at how plate heat exchangers can be used in the production of green hydrogen and in the hydrogen value chain.
Resource center
Still curious?