Budgetary constraints
Minimize your project expenses effectively by implementing strategic cost-saving measures. Adopting efficient planning, and ongoing cost analysis can dramatically reduce unnecessary expenditures.
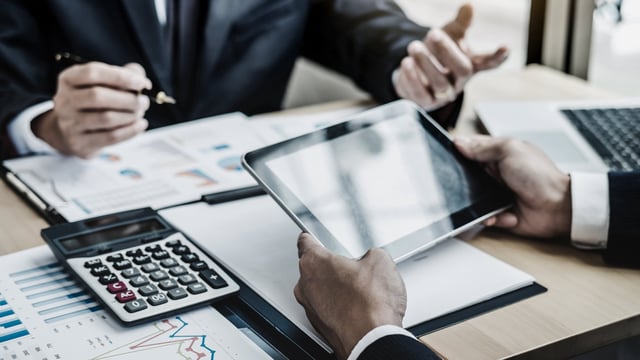
Power plant heat exchangers
Tranter’s plate heat exchangers help improve energy consumption, boost operational effectiveness, and bolster the dependability and eco-friendliness of power generation systems for conventional coal or natural gas fired power plants, nuclear, combined heat and power and renewable energy plants. Heat exchangers are instrumental in power generation processes, playing a crucial role in elevating efficiency, ensuring safety, and promoting environmental protection by heat recovery.
Power generation
Minimize your project expenses effectively by implementing strategic cost-saving measures. Adopting efficient planning, and ongoing cost analysis can dramatically reduce unnecessary expenditures.
With our extensive service center network, we offer quick, localized support, minimizing operational disruptions and boosting both performance and productivity.
Gain immediate, expert advice on streamlining projects to drastically cut down on administration time. Tranter combines small-company agility and customer focus, ensuring personalized attention to every customer's needs.
Power generation
A closed loop of cooling medium, normally water or water/glycol mixture is used for all the different cooling duties in power generation and to dissipate heat from the components of the power plants. The cooling medium is cooled by seawater or lake water in gasketed plate and frame heat exchangers to avoid using corrosive and erosive sea/lake water inside the process. Tranter’s plate and frame heat exchangers are optimal for large cooling medium cooler duties, capable of handling close temperature approaches and large volumes with minimum plot space requirements.
If the power plant location doesn’t have a sea, lake or river nearby, central cooling is done by cooling towers. Tranter’s gasketed plate and frame heat exchangers are employed as cooling tower intermediate cooler. The plate heat exchanger intermediate cooler protects the power plant by keeping the internal cooling water clean.
Conventional power plants that generate heat and electricity by burning fossil fuels such as coal, natural gas, or oil have a great need for efficient and reliable heat exchangers. Tranter’s gasketed and welded plate heat exchangers help optimize steam generation, recovering waste heat, and various lube oil cooling applications to the turbines, transformers and electricity generators, as well as feed water heaters, feedwater and vacuum pump coolers. In combined heat and power plants, Tranter’s plate heat exchangers play an essential role in connecting the plant to the district heating network to ensure the generated heat is reused to the maximum.
Heat exchangers in nuclear power plants transfer heat from the reactor coolant (usually water or a liquid metal) to a secondary loop, where steam is produced without directly exposing it to radioactive materials. Tranter’s gasketed plate and frame heat exchangers are mainly employed in the secondary loop on the nuclear power plant, providing efficient heat recovery and reliable operation and cooling of the plant.
Centralized solar power (CSP) plants use mirrors or lenses to concentrate sunlight onto a receiver, which heats a working fluid (such as molten salt). Tranter’s gasketed and welded plate heat exchangers transfer the heat from the working fluid to water, generating steam for electricity generation.
To reach the NetZero goals, new and existing power plants are looking to reduce the CO2 emissions. Post combustion CO2 capture to power plants involves removing CO2 from gas streams using continuous absorption with regenerable solvents, crucial for reducing greenhouse gas emissions and fighting climate change. Tranter leads in providing heat exchangers for carbon capture, ensuring your plant operates safely and reliably.
Resource center
Energy, Process industries Sustainability
Tranter’s heat exchangers have various applications across many different markets. Let’s take a look at how plate and frame heat exchangers can be used in CO2 capture applications to improve the total economy of the plant.
Energy, Process industries
Tranter’s compact plate heat exchangers are used in various energy intense industrial applications. Let’s take a look at how plate heat exchangers can be used in the production of green hydrogen and in the hydrogen value chain.
Sustainability Energy, heating and cooling Energy, Process industries
Explore our comprehensive brochure to delve deeper into Tranter and discover the wide range of offerings we provide.
Resource center
Our comprehensive understanding of heat exchangers goes beyond just maintenance and usage. We offer tailored recommendations and innovative solutions to optimize your system's performance, reduce energy consumption, and extend the lifespan of your equipment. Our goal is to not only enhance your operational efficiency but also to ensure the long-term health and reliability of your heat exchangers. Trust Tranter to provide expert insights that keep your systems running smoothly and cost-effectively.
Still curious?