Communication
Gain immediate, expert advice on streamlining projects to drastically cut down on administration time. Tranter combines small-company agility and customer focus, ensuring personalized attention to every customer's needs.
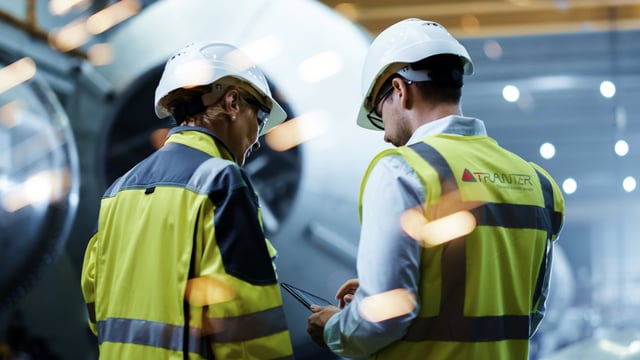
Energy efficiency of your heat exchanger
Tranter’s gasketed and welded plate heat exchangers are used in various applications in petrochemical and chemicals plants, driving innovations in energy efficiency, setting new benchmarks in safety, and being instrumental to help make the industry more sustainable.
Petrochemicals and chemicals
Gain immediate, expert advice on streamlining projects to drastically cut down on administration time. Tranter combines small-company agility and customer focus, ensuring personalized attention to every customer's needs.
With our extensive service center network, we offer quick, localized support, minimizing operational disruptions and boosting both performance and productivity.
We understand how critical it is for our customers to meet or even surpass project timelines. It's for this reason we are committed to ensuring deliveries are not just on time, but guaranteed to be prompt.
Petrochemicals and chemicals
Ethylene oxide is crucial in the petrochemical industry as an intermediate in the manufacturing of plastics, fibers and other downstream chemicals and ethylene glycols, marking its importance in the global chemical supply chain. Tranter’s gasketed and welded plate heat exchangers are employed in process heating and cooling applications as well as in heat recovery of the recycled water, improving the economy and sustainability of the plant. Tranter have experience with many major process licensors such as SD (Scientific Design), shell and dow chemicals.
Various production processes exist for polyethylene and polypropylene with some general similarities, one being the importance of efficient and reliable plate heat exchangers. Tranter’s gasketed an welded plate heat exchangers are employed for jacket and reaction mixture cooling as overhead condensers on the ethylene purification column and in the solvent recovery system. Tranter’s wide gap plate heat exchangers are good fit for cooling of pellet water, mixtures and extruders.
Petrochemicals and chemicals
Aromatics, which includes benzene, toluene and xylene, are needed to produce an extensive range of everyday products. Aromatics are commonly produced by chemical synthesis. Tranter’s gasketed and welded plate heat exchangers are essential in this energy intense process as condensers, trim coolers, interchangers/preheaters, and reboilers.
Ensuring precise temperature regulation of corrosive liquids or the condensation of corrosive gases necessitates the use of heat exchangers. These devices adeptly transfer energy between fluid streams, safeguarding against corrosion. In the chemical sector, heat exchangers find diverse applications tailored to specific needs.
In the production of polymers and plastics from petrochemical feedstocks, heat exchangers are used to control temperatures during polymerization reactions. They ensure that the reaction proceeds optimally without overheating or cooling too much.
A closed loop of cooling medium, normally water or water/glycol mixture is used for all the different cooling duties in petrochemical and chemical plants. The cooling medium is cooled by seawater in gasketed plate and frame heat exchangers to avoid using corrosive and erosive seawater inside the process. Tranter’s plate and frame heat exchangers are optimal for large cooling medium cooler duties, capable of handling close temperature approaches and large volumes with minimum plot space requirements. The wastewater from the plants is treated to be reintroduced to the process or back to the source. Plate heat exchangers are a good choice for wastewater treatment plants as they reducing fouling tendencies and are easy to open for maintenance.
To reach the NetZero goals, petrochemical and chemical plants are looking to reduce the CO2 emissions. Post combustion CO2 capture to petrochemical and chemical plants involves removing CO2 from gas streams using continuous absorption with regenerable solvents, crucial for reducing greenhouse gas emissions and fighting climate change. Tranter leads in providing heat exchangers for carbon capture, ensuring your plant operates safely and reliably.
Resource center
Energy, heating and cooling Sustainability
The digitalization mega trend has resulted in exponential growth of data centers. Let’s take a look at how Tranter’s plate and frame heat exchangers can be used to make the datacenters more sustainable.
Energy, Process industries Sustainability
Tranter’s heat exchangers have various applications across many different markets. Let’s take a look at how plate and frame heat exchangers can be used in CO2 capture applications to improve the total economy of the plant.
Energy, Process industries
Tranter’s compact plate heat exchangers are used in various energy intense industrial applications. Let’s take a look at how plate heat exchangers can be used in the production of green hydrogen and in the hydrogen value chain.
Our comprehensive understanding of heat exchangers goes beyond just maintenance and usage. We offer tailored recommendations and innovative solutions to optimize your system's performance, reduce energy consumption, and extend the lifespan of your equipment. Our goal is to not only enhance your operational efficiency but also to ensure the long-term health and reliability of your heat exchangers. Trust Tranter to provide expert insights that keep your systems running smoothly and cost-effectively.
Resource center
Still curious?