On time deliveries
We understand how critical it is for our customers to meet or even surpass project timelines. It's for this reason we are committed to ensuring deliveries are not just on time, but guaranteed to be prompt.
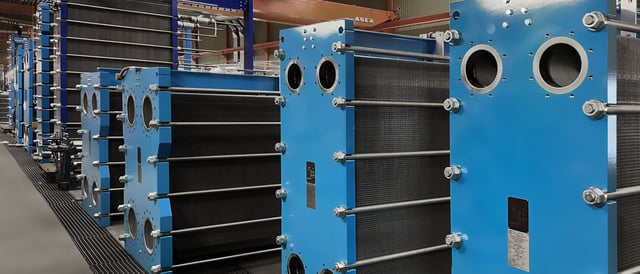
Heat exchangers for genset and cogeneration
The genset and cogeneration industries play essential roles in meeting diverse energy needs, providing reliable power generation, energy efficiency, and resilience solutions for a wide range of applications. Heat exchangers help optimize energy utilization, enhance system efficiency, and reduce environmental impact by capturing and utilizing waste heat for beneficial purposes.
Leveraging the full potential of energy-efficient cogeneration, also known as combined heat and power (CHP), represents a highly effective and efficient approach to power generation, enabling enhanced energy utilization. Tranter has long expertise designing heat exchangers for these applications.
genset and cogeneration
We understand how critical it is for our customers to meet or even surpass project timelines. It's for this reason we are committed to ensuring deliveries are not just on time, but guaranteed to be prompt.
Our commitment lies in harmonizing work-life equilibrium for your team, guaranteeing that tasks are completed efficiently and on schedule.
Minimize your project expenses effectively by implementing strategic cost-saving measures. Adopting efficient planning, and ongoing cost analysis can dramatically reduce unnecessary expenditures.
Genset and Cogeneration
In gensets powered by internal combustion engines, such as diesel or gas engines, heat exchangers are used to cool the engine coolant. This prevents the engine from overheating during operation, ensuring optimal performance and longevity.
Cogeneration diesel engines, or diesel-fired cogeneration systems, generate electricity and thermal energy from diesel fuel. They use internal combustion engines to power generators and capture waste heat for heating, cooling, or other thermal uses. Tranter’s plate and frame heat exchangers provide precise temperature control in heating and cooling duties of the fluids in the process, ensuring safe and reliable operation of the diesel engines and the cogeneration system.
The higher the temperature of the waste heat, the more applications it can be used for. Low temperature waste heat can also be recovered and be used to for example space heating, green houses and fish farms where plate heat exchangers play an essential part as heat recovery heat exchangers.
Resource center
Energy, heating and cooling Sustainability
The digitalization mega trend has resulted in exponential growth of data centers. Let’s take a look at how Tranter’s plate and frame heat exchangers can be used to make the datacenters more sustainable.
Energy, Process industries Sustainability
Tranter’s heat exchangers have various applications across many different markets. Let’s take a look at how plate and frame heat exchangers can be used in CO2 capture applications to improve the total economy of the plant.
Sustainability Energy, heating and cooling Energy, Process industries
Explore our comprehensive brochure to delve deeper into Tranter and discover the wide range of offerings we provide.
Resource center
Energy, Process industries Marine and shipbuilding Sustainability
Energy, Process industries Marine and shipbuilding Sustainability
Resource center
Still curious?