Heat exchanger sizes
When it comes to heat exchangers, size isn’t just about dimensions – it’s about performance, efficiency, and making the right call for your setup. Picking the biggest or smallest unit off the shelf won’t cut it. You need to optimize for what actually matters: heat transfer, energy use, and space constraints. Here, we’re diving into exactly that (and how to get it right).
Size or sizing – what’s the difference?
People throw around the terms size and sizing like they mean the same thing – but they don’t. Size refers to the physical footprint of the heat exchanger: height, width, depth, and how much space it takes up. Sizing, though, is about figuring out the right dimensions for your specific application.
Bigger doesn’t always mean better. Sure, a larger heat exchanger can transfer more heat, but other factors come into play:
- Heat load: How much heat needs to be moved?
- Flow rates: How fast are the fluids moving through the exchanger?
- Temperature differential: What’s the required temp drop?
- Material and design: Some materials and configurations boost efficiency, meaning you might not need a massive unit.
For example, a gasketed plate heat exchanger might outshine a bulky shell-and-tube model thanks to its design efficiency.
When size actually matters
Can you just put the same heat exchanger into any system? Absolutely not. Different industries have different constraints, and size plays a crucial role in choosing the right one.
For tight spaces – like HVAC units, marine vessels, and automotive cooling – you need compact heat exchangers that deliver serious performance without hogging room. But if you’re dealing with power plants, chemical processing, or heavy-duty industrial applications, you’ll likely need larger units to handle massive heat loads.
Applications where proportions can matter
- HVAC systems: Compact designs keep buildings cool without wasting space.
- Automotive & aerospace: Lightweight and space-efficient models are a must.
- Oil & gas, chemical processing: Large-scale operations need big, rugged exchangers.
- Data centers: High-efficiency cooling systems demand the right balance between size and performance.
Plus, different heat exchanger types take up space differently. Plate heat exchangers tend to be more compact, while shell-and-tube models are bulkier but powerful.
Large vs. small heat exchangers
When choosing between large and small heat exchangers, it’s all about trade-offs. Here’s how they stack up:
Big heat exchangers
✔️ Handle higher heat loads effortlessly
✔️ Lower pressure drops, making them great for heavy-duty applications
✔️ Longer lifespan due to less stress on components
❌ Take up more space—installation can be a headache
❌ Higher upfront cost
❌ Slower to install and integrate
Small Heat exchangers
✔️ Space-saving and lightweight
✔️ More energy-efficient for low-to-medium loads
✔️ Easier to maintain and replace
❌ Might not handle large heat loads effectively
❌ Higher pressure drops can reduce efficiency
❌ Might need multiple units to match a larger exchanger’s performance
For industries balancing space and performance, compact heat exchangers (like brazed-plate or serpentine designs) are changing the game.
How to size a heat exchanger the right way
If you want your heat exchanger to actually perform as expected, you need to size it properly. Here’s how to do it:
The essentials of heat exchanger sizing:
- Calculate the heat load – Measure the total heat transfer needed (BTUs/hr or kW).
- Define your temp goals – What’s the required temperature difference?
- Find the Log Mean Temperature Difference (LMTD) – This tells you the heat transfer efficiency.
- Factor in flow rates – Ensure your exchanger can handle the necessary fluid volumes.
- Pick the right type – Plate, shell-and-tube, finned-tube? Each has its own benefits.
- Consider fouling resistance – Heat exchangers get dirty over time, so plan accordingly.
Want a deep dive into the calculations? Check out our dedicated guide on plate heat exchanger sizing for a more technical breakdown.
Final thoughts
Choosing the right heat exchanger size is about maximizing efficiency, optimizing space, and keeping operating costs in check. Whether you’re after a compact, high-performance model for a space-restricted setup or a heavy-duty unit for large-scale heat transfer, knowing the difference between size and sizing is key.
By following proper sizing methods and considering industry-specific needs, you’ll end up with a heat exchanger that delivers on both performance and longevity.
Resource center
Introducing ThermoFit™ DN150 plate series
Energy, Process industries Marine and shipbuilding Sustainability
Plate series introduction: The GT-165
resource center
Explore our latest guides and literature
Energy, heating and cooling Sustainability
Tranter heat exchangers in the sustainable data centers
The digitalization mega trend has resulted in exponential growth of data centers. Let’s take a look at how Tranter’s plate and frame heat exchangers can be used to make the datacenters more sustainable.
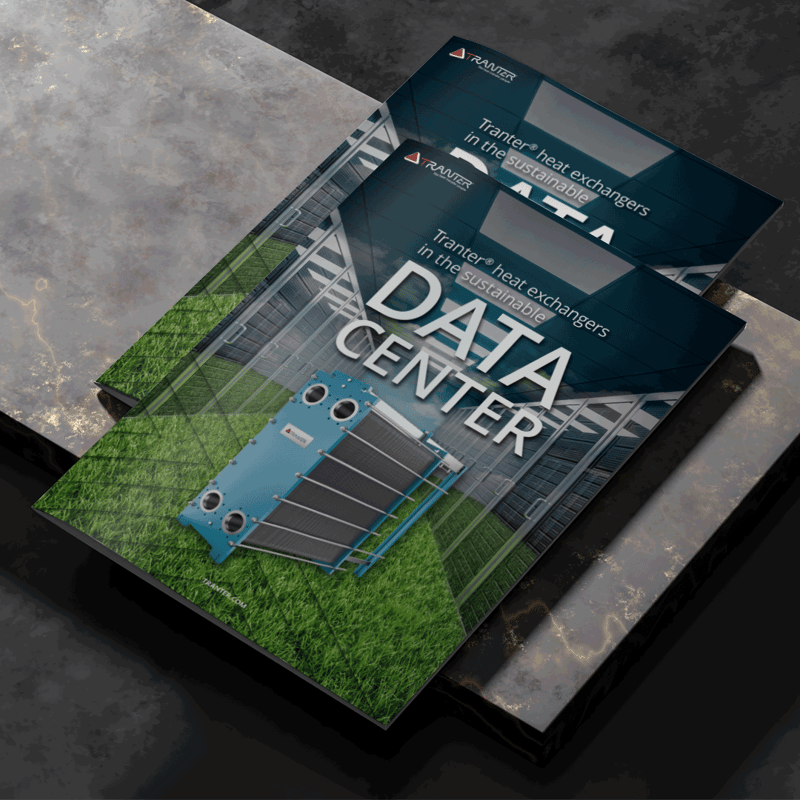
Energy, Process industries Sustainability
Heat exchangers for post combustion carbon capture applications
Tranter’s heat exchangers have various applications across many different markets. Let’s take a look at how plate and frame heat exchangers can be used in CO2 capture applications to improve the total economy of the plant.
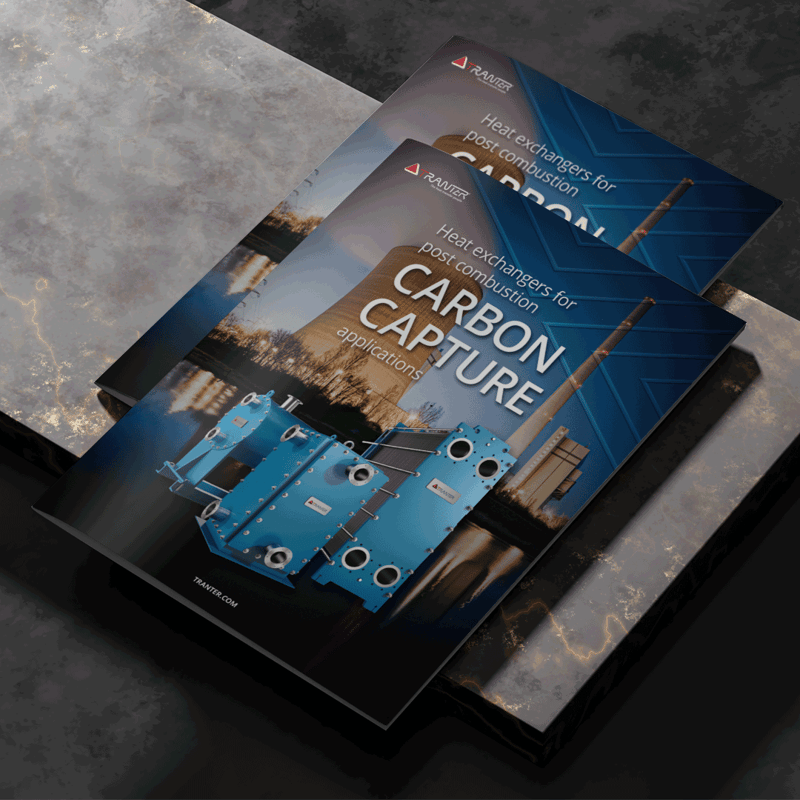
Energy, Process industries
Tranter heat exchangers in green hydrogen production
Tranter’s compact plate heat exchangers are used in various energy intense industrial applications. Let’s take a look at how plate heat exchangers can be used in the production of green hydrogen and in the hydrogen value chain.
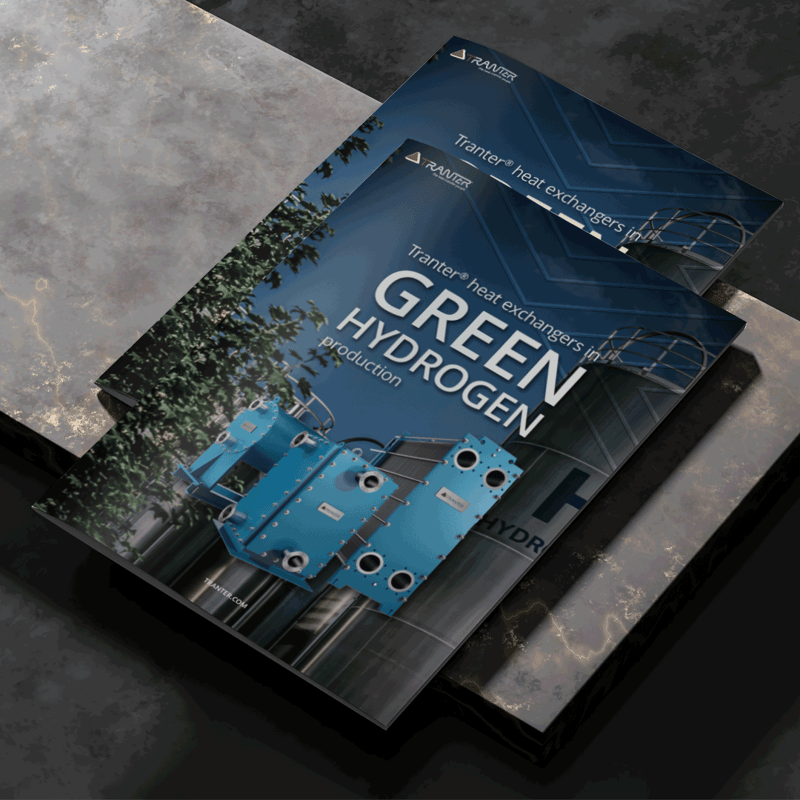
Sustainability Energy, heating and cooling Energy, Process industries
Bringing efficiency to heat transfer
Explore our comprehensive brochure to delve deeper into Tranter and discover the wide range of offerings we provide.
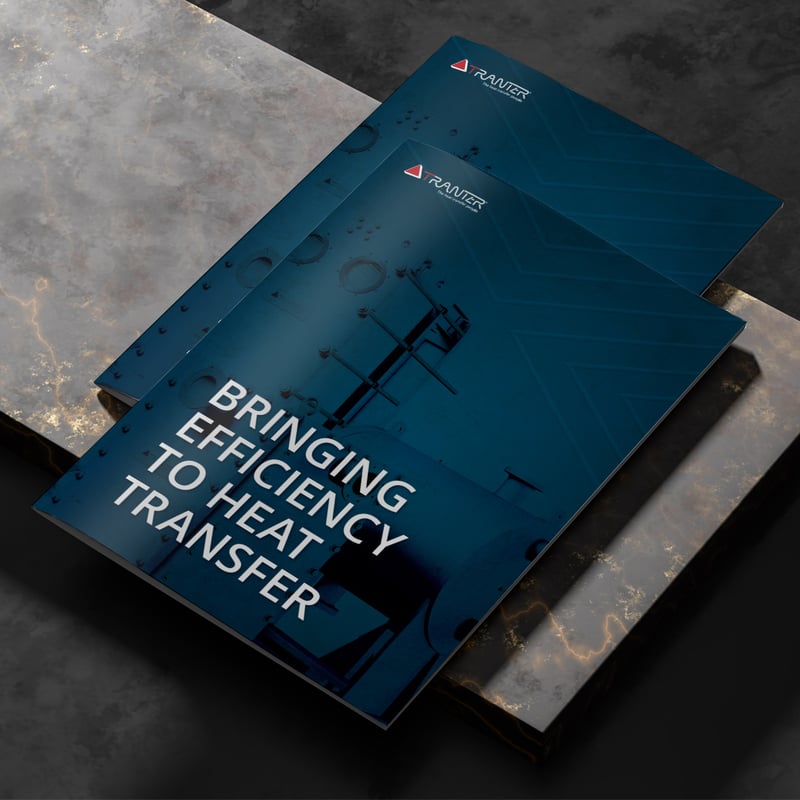
Parts and services
Restoring plate heat exchangers to optimal performance
With regular service and maintenance you will keep control of your heat exchangers conditions and maintain optimal performance. Learn more from this simplified quick guide.
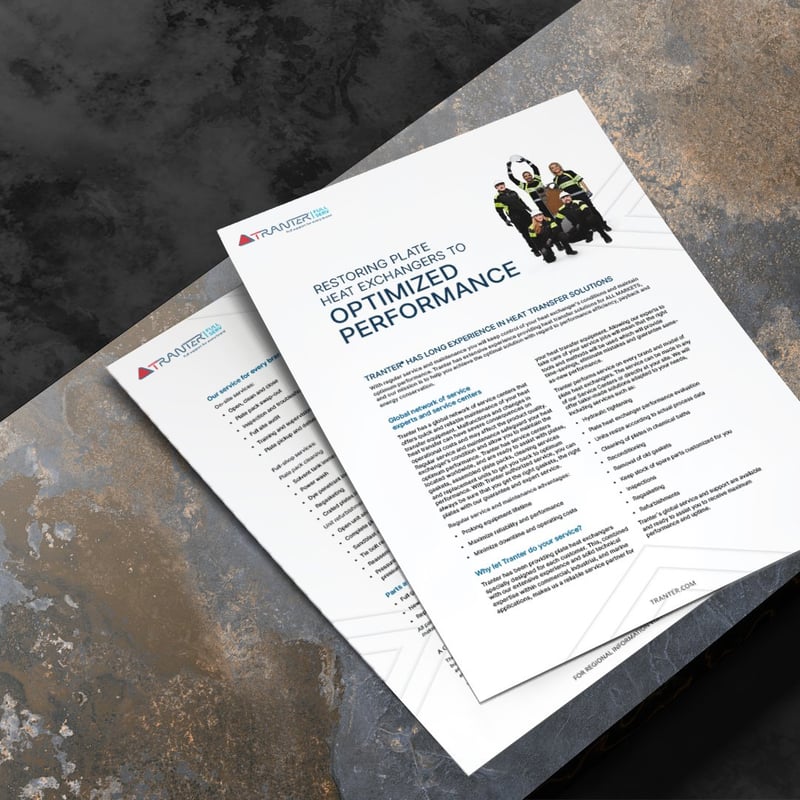
Energy, heating and cooling Energy, Process industries Marine and shipbuilding
The Welded block heat exchanger - NovusBloc®
For increased durability and energy efficiency. Get some more insights to our welded block heat exchanger with this guide.
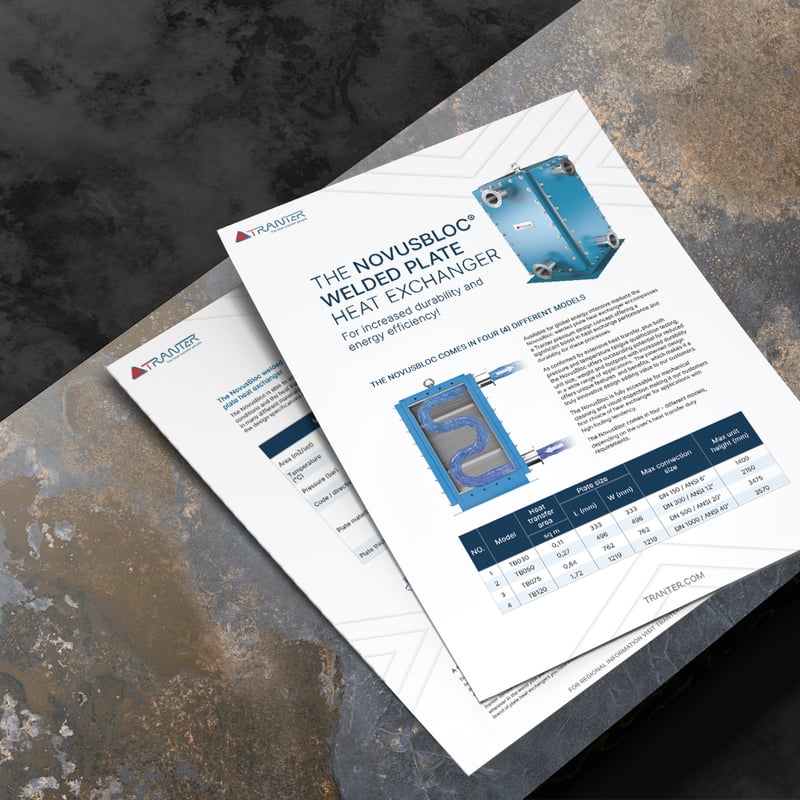
Energy, heating and cooling Energy, Process industries Marine and shipbuilding
When conditions are tough, think plates instead of tubes
Now you can obtain the thermal efficiency and compactness of gasketed heat exchangers in elevated pressure/high-and-low temperature applications. Learn more about our shell and plate heat exchanger.
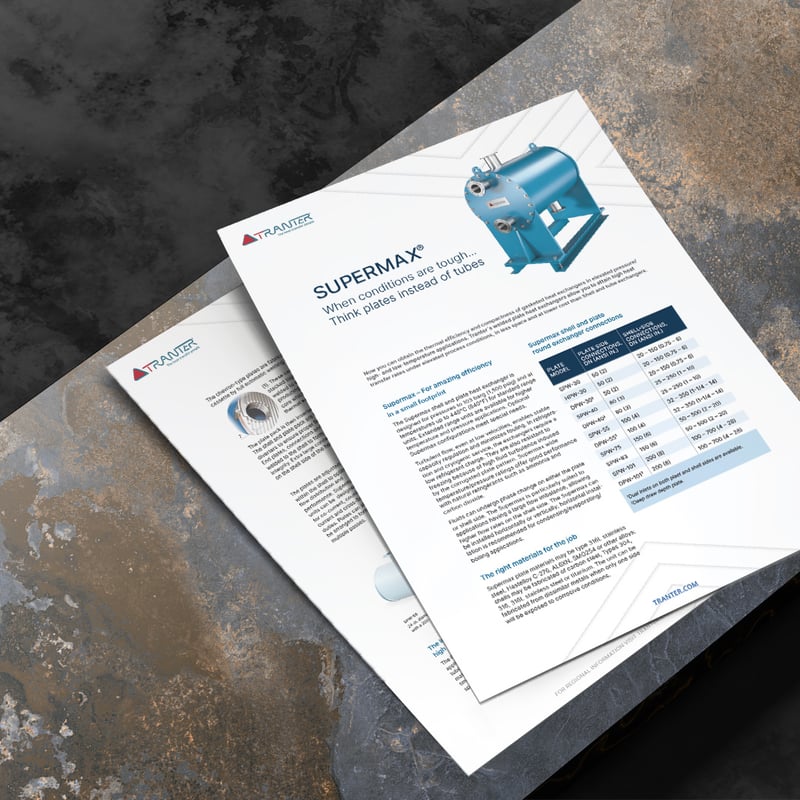
Energy, heating and cooling Energy, Process industries Sustainability
Plate and frame for maximum efficiency
Optimum performance is a promise Tranter has been fulfilling for many decades with the Superchanger® plate and frame heat exchanger.
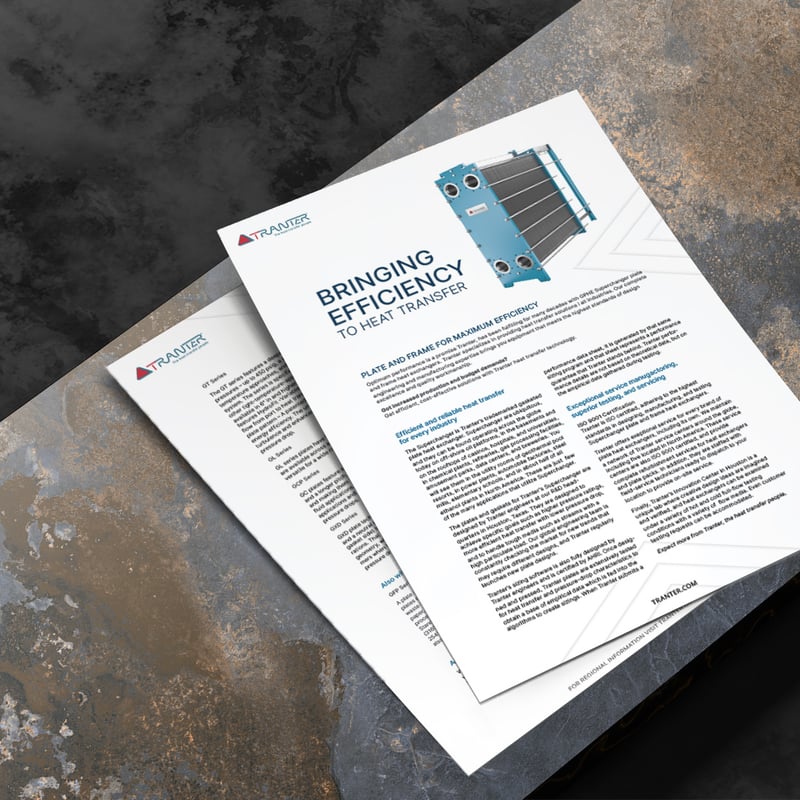
Energy, heating and cooling
Guide: Selecting the right heat exchanger for your heating and cooling application
Selecting a heat exchanger is not just about finding an option that fits within your budget. Your choice should strike an optimal balance between cost and performance. Otherwise, you could end up with a unit that’s not designed for its purpose. This mistake can be costly. So, how do you know which exchanger is right for you?
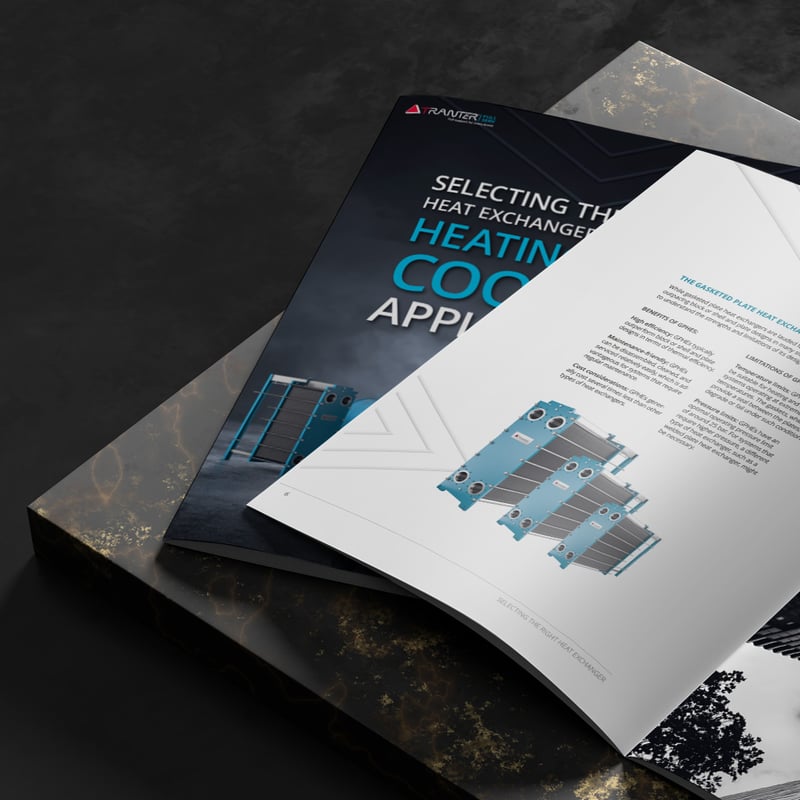
Parts and services
Guide: 8 steps to improve (and maintain) heat exchanger efficiency
Are you tired of feeling like your heat exchanger is draining your wallet like a car engine left running all night? Our guide walks you through the steps you need to take – from pre-purchase and design to maintenance – to get the most out of your heat exchanger.
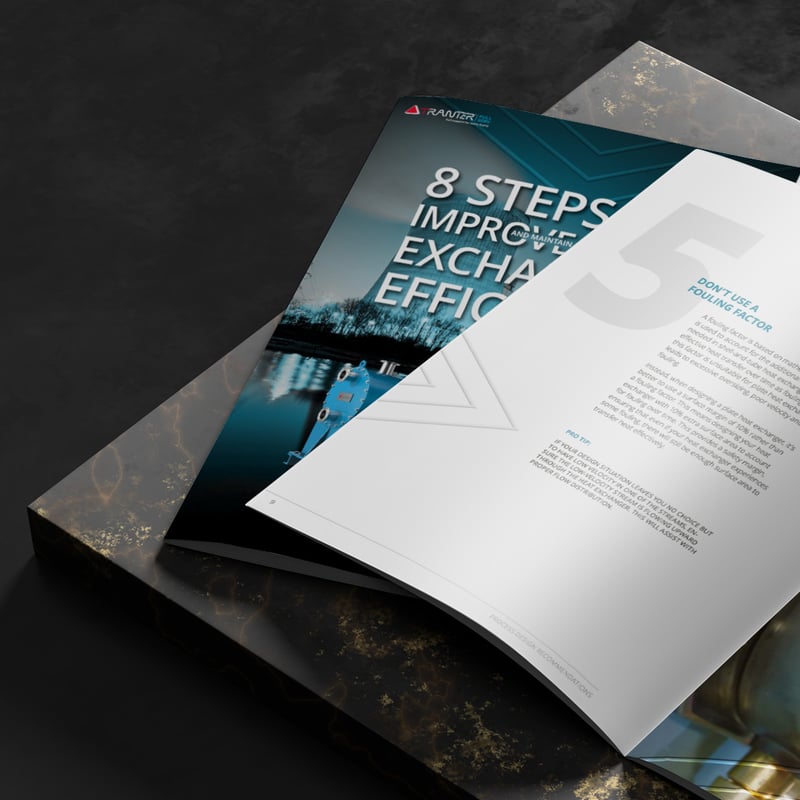
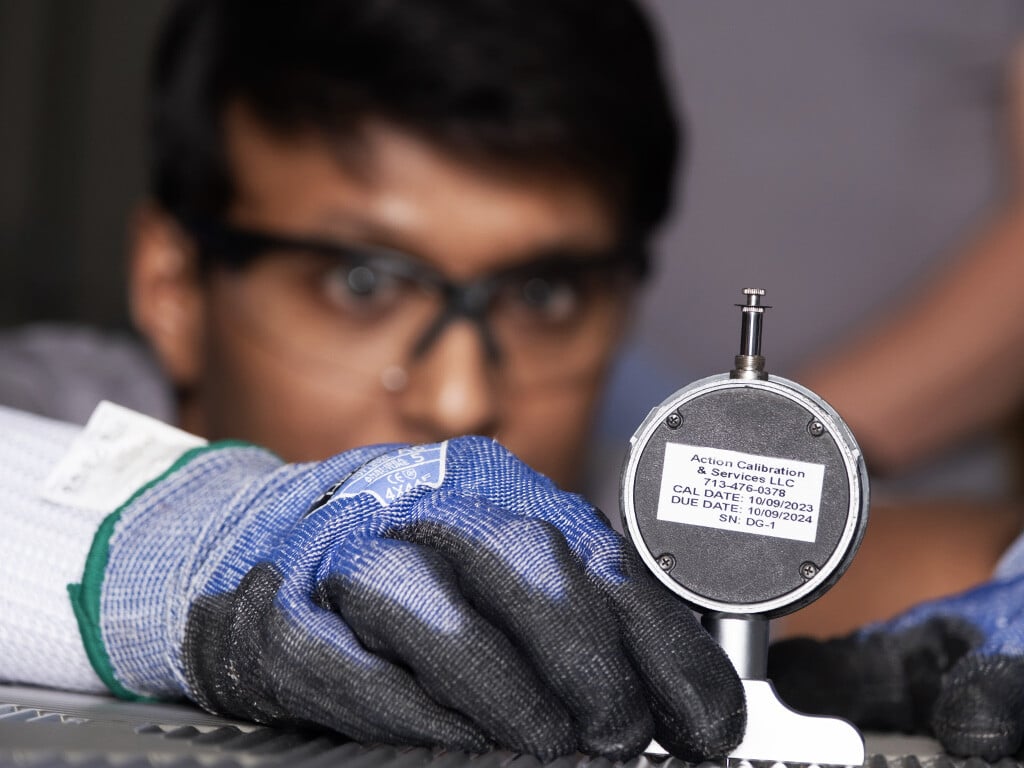
Innovation and development
Resource center
Discover our customer cases
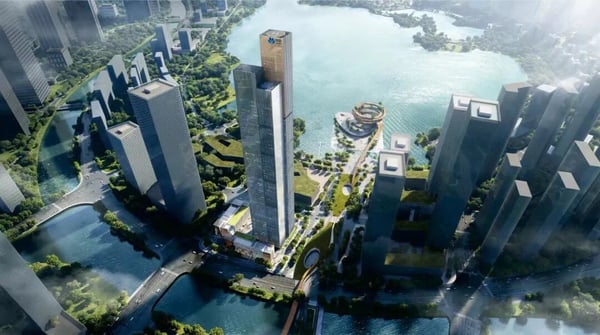
Energy, Heating and cooling
Tranter China joins hands with Jinmao to create a new model of sustainability

Marine and shipbuilding
Daewoo opts for Tranter’s plate heat exchangers for world’s biggest container ships
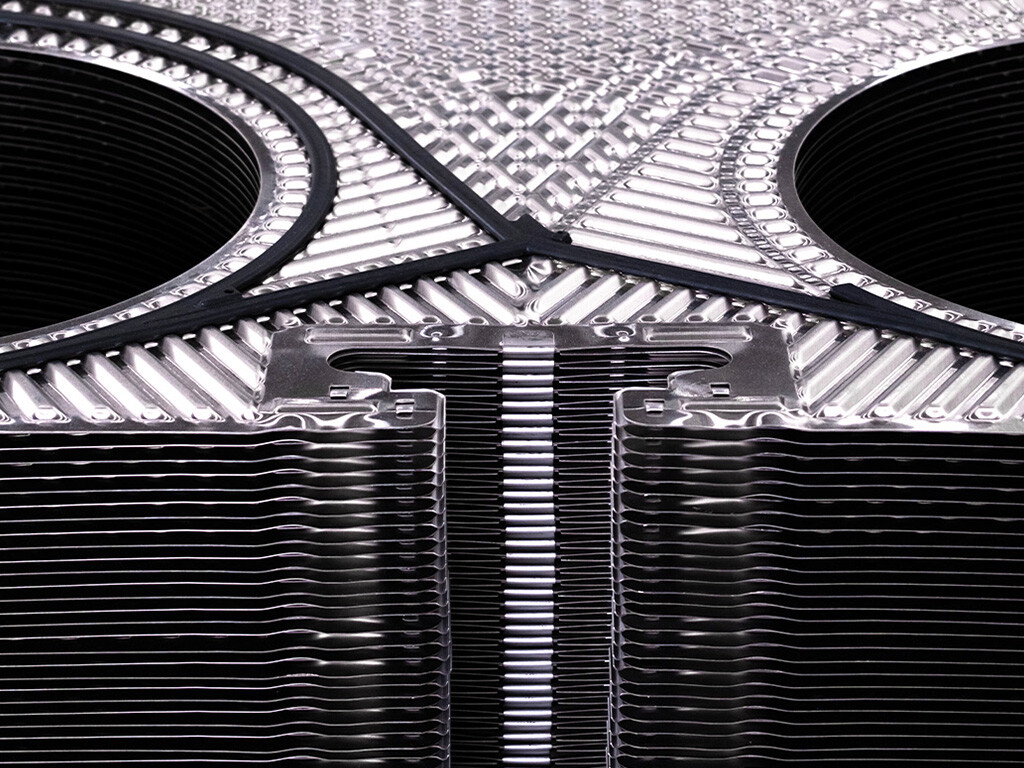
TRANTER FULLSERV® – Full support for every brand
Are you considering acquiring heat exchangers?
Contact us for more information!
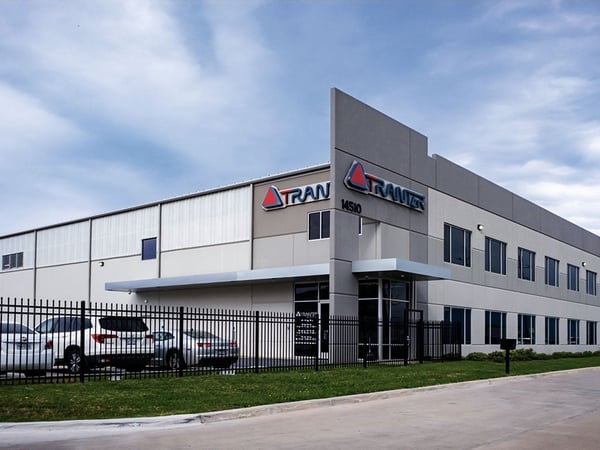