Supermax® units excel as solvent condensers in pharmaceutical manufacturing
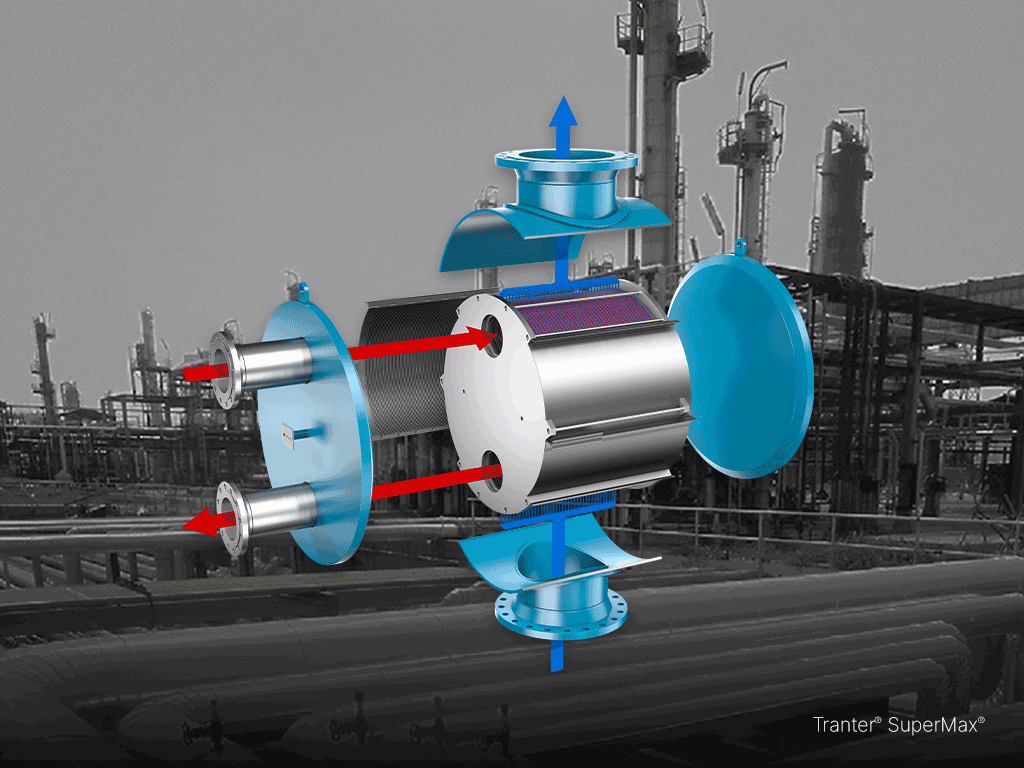
Supermax units are earning preference over shell and tube exchangers for their lower cost, rapid delivery, smaller footprint and easier maintenance.
In processes involving In processes involving batch reactors with one batch reactors with one or more organic solvents, the Supermax all-welded shell & plate unit offers potential for improved performance and efficiency. The opportunity for a significant solution can be quite substantial, since multiple condensers are often used on each batch reactor as primary and secondary condensers and vent condensers.
Tranter recently received a significant contract for Supermax condensers from a leading bulk pharmaceutical producer in Hyderabad, India. The contract consisted of many SM-22 units, each with a surface area less than 120 ft2 (12 m2), and several SM-07 units, each with less than 60 ft2 (6 m2) of surface area. All units were supplied with the removable core option.
The application
Batch reactor capacity ranges from 265 to 1585 gal (1000 to 6000 liters). Solvents used include methanol, toluene, dichloromethane, xylene, tetrahydrofuran, chloroform and others. Used only to dissolve the reactants, products and byproducts, the solvents must be and byproducts, the solvents must be recycled for efficiency and environ- recycled for efficiency and environmental reasons. Some processes use mental reasons. Some processes use the condensers to cycle the solvents the condensers to cycle the solvents back to the reactor; some collect back to the reactor; some collect the condensate in tanks for the condensate in tanks for reuse. In some processes, condensable reaction byproducts are entrained with products are entrained with the solvent vapor.
Upon completion of the various reactions in the steam-heated, jacketed reactors, the solvents are vaporized and condensed by a two-stage, primary and secondary condenser arrangement. A Supermax secondary condenser, or sub cooler, is often used with chiller water media to condense these volatile organic compounds (VOCs). Noncondensibles or refrigerants are sometimes removed by a thermal oxidizer.
The opportunity
Conventionally, each reactor has S&T units as primary and secondary condensers, sized in accordance with reactor capacity. These units are relatively slow to respond; reactors with Supermax units in many cases have a shorter vaporization/condensation cycle time, which can raise plant capacity. Additionally, the much larger S&T units require more steel, which raises their purchase price and makes necessary more elaborate and expensive support structures. Maintenance of S&T units is more difficult, considering that the tube bundle pulling process requires more labor and space than removing the Supermax cover/plate pack assembly for descaling. These Supermax advantages make reactor solvent condenser applications an attractive optimization strategy for pharmaceuticals and chemical process industries. In some cases, there may be an opportunity to replace slowresponding S&T units in the reactor thermal control loop with Superchanger plate and frame or Supermax all-welded units. Tranter plate HEs, with their smaller hold-up volume, can heat the jacketed reactor to the setpoint faster, conserve costly heat transfer fluids, and control reaction temperature more precisely. The benefits better yield, lower energy consumption and less off-grade production.
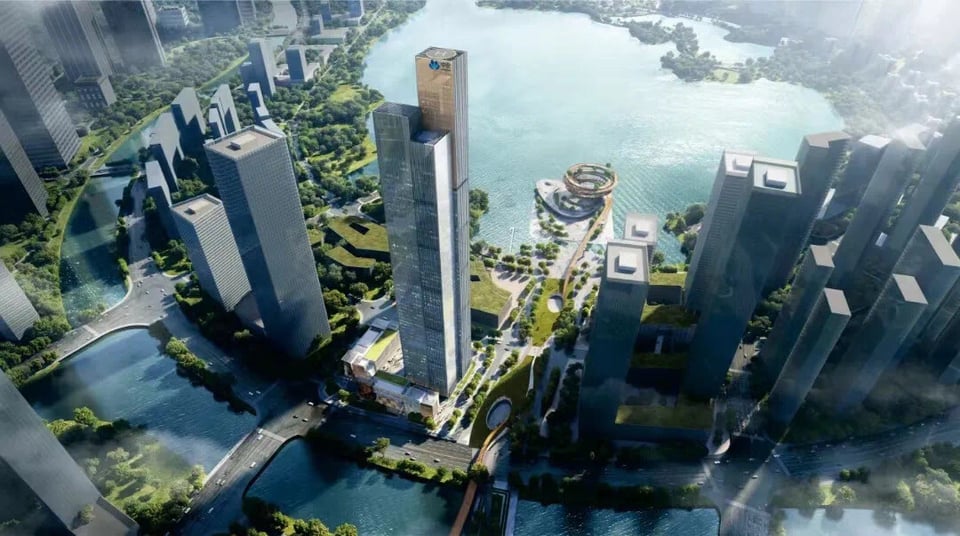
latest customer case
Tranter China joins hands with Jinmao to create a new model of sustainability
Energy, Heating and cooling