Supermax® exchangers replace shell and tube units as deck heaters
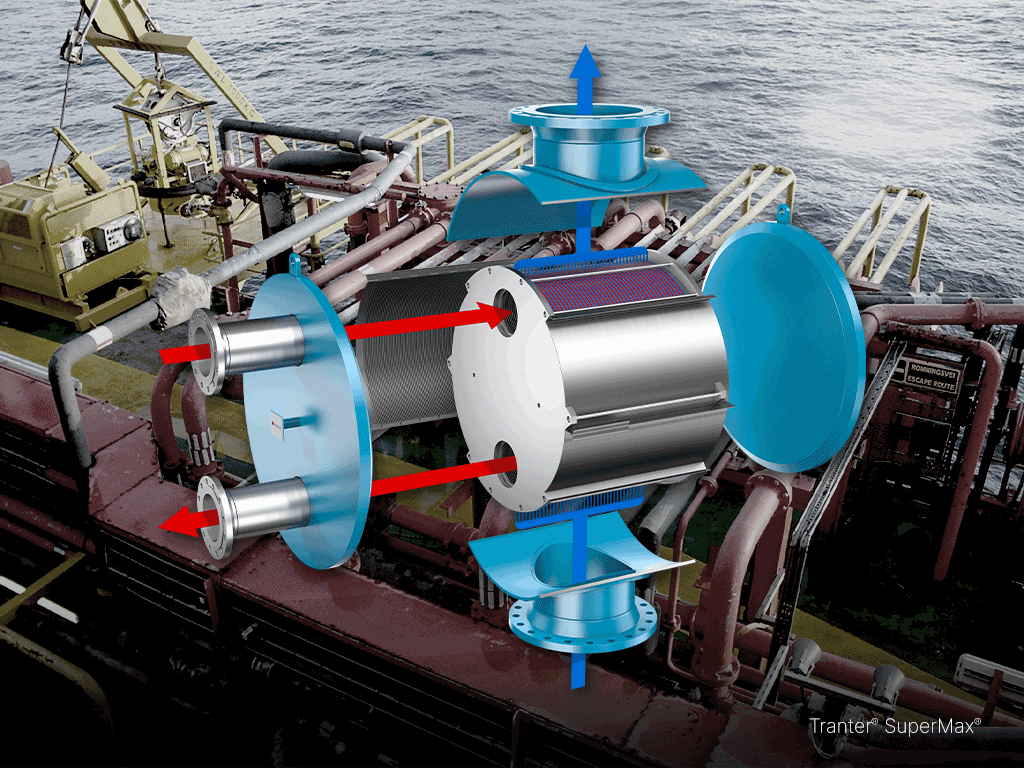
Shell and plate exchangers do more with less — less size, weight and cost — with faster delivery. Add to these benefits easier maintenance, and you get outstanding life cycle cost performance.
An owner of U.S.-flag petroleum carriers operates self-propelled vessels transporting petroleum products, chemicals and crude oil along the Atlantic, Gulf and Pacific coasts, and Alaska. The company’s double-hull tankers had been using shell and tube heat exchangers as steam-heated deck heaters. The heaters maintain bunker C fuel oil at an elevated temperature during transport to enable effi cient unloading upon arrival at ports and terminals. The heating system constantly pumps the heavy oil from the cargo holds through the deck heaters until it is unloaded at its destination. Similar heating systems are used to aid transportation of other viscous liquids, such as crude oil, vegetable oil and certain chemicals.
The shell and tube deck heaters had shown themselves to be large, heavy, slow to respond to heating demand and also to be maintenance burdens. When the time came to replace 14 of them throughout the fleet, the ship owners were receptive to consideration of alternate deck heater technologies.
Converting to plate heat exchanger technology
During their evaluations, the ship owners became impressed with the benefits resulting from the higher efficiency of plate heat exchangers compared to S&T units. They found that the Tranter Supermax shell and plate unit, with its higher heat transfer rate, required less metal and size. This contributed to a shorter manufacturing time and lower material cost. It also afforded advantages in lower topside weight, smaller footprint and ease of maintenance.
Maintenance benefits over shell and tube
At maintenance time, the removable core Supermax is easier to open and remove the plate pack assembly than the S&T unit. Additionally, the high flow turbulence afforded by the plate design was judged to offer superior scaling and fouling resistance. At the same time, pressure drop across the exchanger through the product channel was only 9 psi, helping reduce energy consumption for pumping. In the face of these plate heat exchanger benefits, the decision became easy. The ship owner selected Supermax for its short delivery lead time, lower cost, more compact size and host of operational benefits.
The Supermax shell and plate exchanger reduces topside footprint and mass because of its higher heat transfer efficiency than shell and tube units.
Supermax deck heaters by the numbers
PLATE SIDE |
SHELL SIDE |
|||
Inlet | Outlet | Inlet | Outlet | |
Temperature, °C (°F) | 55 (131) | 64 (148) | 170 (338) | 170 (338) |
Fluids | Heavy fuel oil | Steam | ||
Viscosity, cP | 181.7 | |||
Flow rate, litres/min (gpm) | 2332 (616) | |||
Mass flow rate, kg/hr (lb/hr) | 133,450 (294,203) | 1054 (2324) | ||
Pressure, bar (psi) | 7 (102) | |||
Heat transfer rate, kJ/hr (BTU/hr) | 2,159,786 (2,047,082) | |||
U value, kJ/(hr•m2•°C) [Btu/(hr•ft2•°F)] | 1766 (87) | |||
Heat transfer surface area, m2 (ft2) | <11 (<120) | |||
Design temperature, °C (°F) | 184 (364) | |||
Design pressure, bar (psi) | 16 (233) | |||
Plate material/shell material | 316LSS/Marine-Coated Carbon Steel | |||
Unit weight, kg (lb) | 232 (512) | |||
Overall dimensions LxWxH, mm (in.) | 864 x 584 x 965 (34 x 23 x 38) |
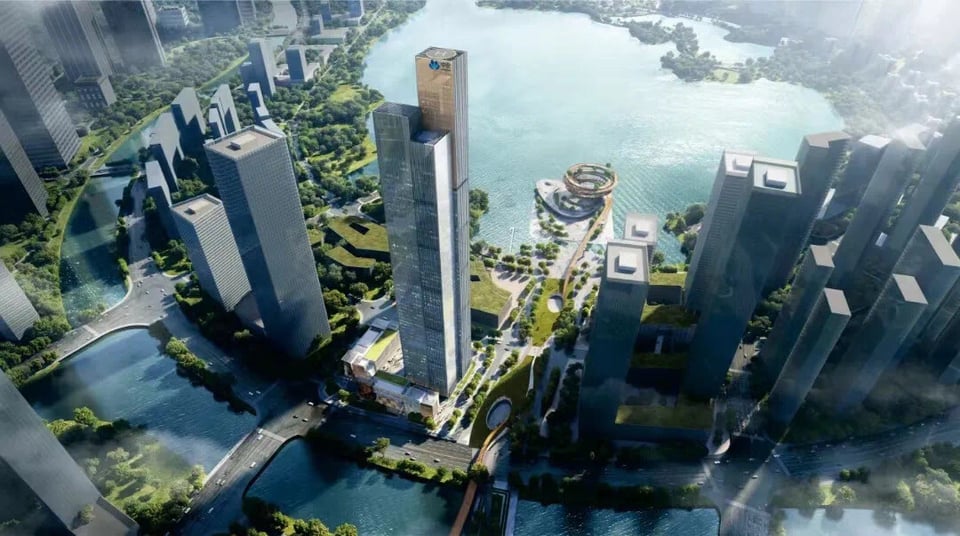
latest customer case
Tranter China joins hands with Jinmao to create a new model of sustainability
Energy, Heating and cooling