Optimizing closed cycle cooling performance with less pumping load and smaller footprint
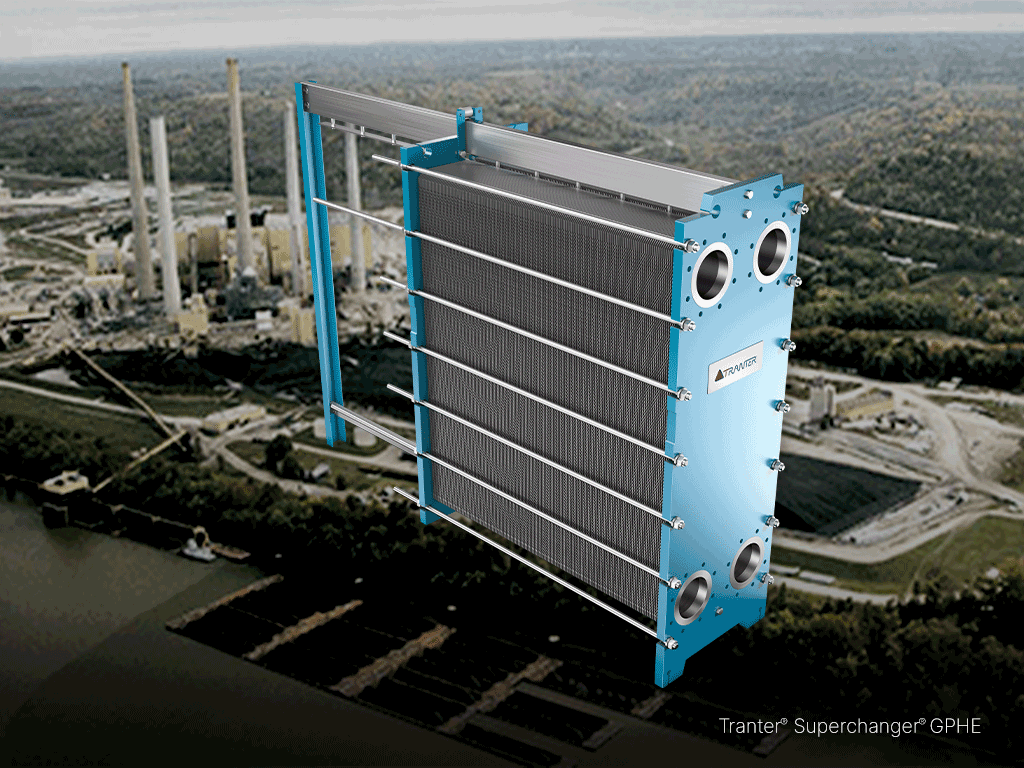
Superchanger® plate and frame exchangers’ heat transfer efficiency serves cooling applications well in constricted power houses
Spurlock power station, located in Maysville, KY, on the Ohio River, is the largest plant owned by East Kentucky Power Cooperative. Spurlock is a four-unit, coal-fired baseload facility generating 1,371 MW net. In april 2005 Spurlock started up the Unit 3 268-MW unit using clean coal technology, particularly a circulating fluidized bed (CFB) furnace section in its power boiler. The similarly sized CFB unit 4 went on line in 2009. Units 3 and 4 rank as among the cleanest coal-powered units in the nation and the cleanest in Kentucky. Spurlock has consistently practiced excellent environmental stewardship. In recent years, nearly $600 million in new environmental-control equipment has been added at Spurlock station.
Cooling machinery more efficiently
In character with the environmental stewardship provided by tight emissions control, the Spurlock station has taken measures to reduce its own internal energy consumption. One strategy has been to install Superchanger GXD-085 plate and frame heat exchangers in several closed cycle cooling loops. These USA-made units can be furnished in a weld neck, flanged design or with studded ports.
Reduced pumping load, less space
The close temperature approach of these highly efficient exchangers reduces the volume of cooling water required to keep various types of equipment within operating temperature specifications. Less volume means less flow and reduced pumping energy demand, which saves power and fuel. This means better thermal efficiency throughout the power station and improved net power output to the cooperatives. Another benefit is the compact footprint of the highly efficient Superchanger. These units can fit in very tight boiler house spaces and make pipefitting and service much simpler tasks. These units can even be assembled in place after delivery of component pieces through manways. Where application conditions exceed the capabilities of gaskets, the Tranter Supermax shell and plate exchanger is a proven alternative, providing significant cooling volume and footprint advantages over conventional shell and tube units
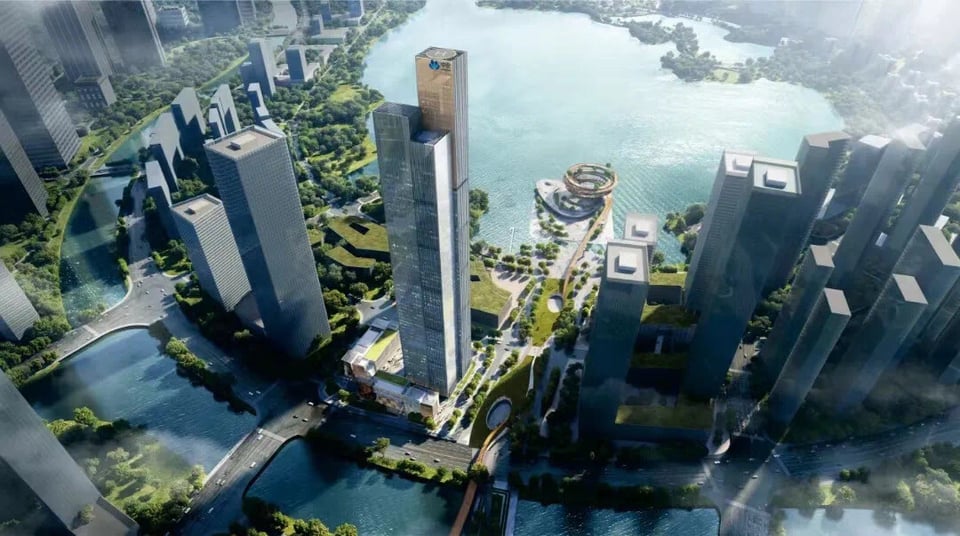
latest customer case
Tranter China joins hands with Jinmao to create a new model of sustainability
Energy, Heating and cooling