Heating the feedwater that keeps the blades turning
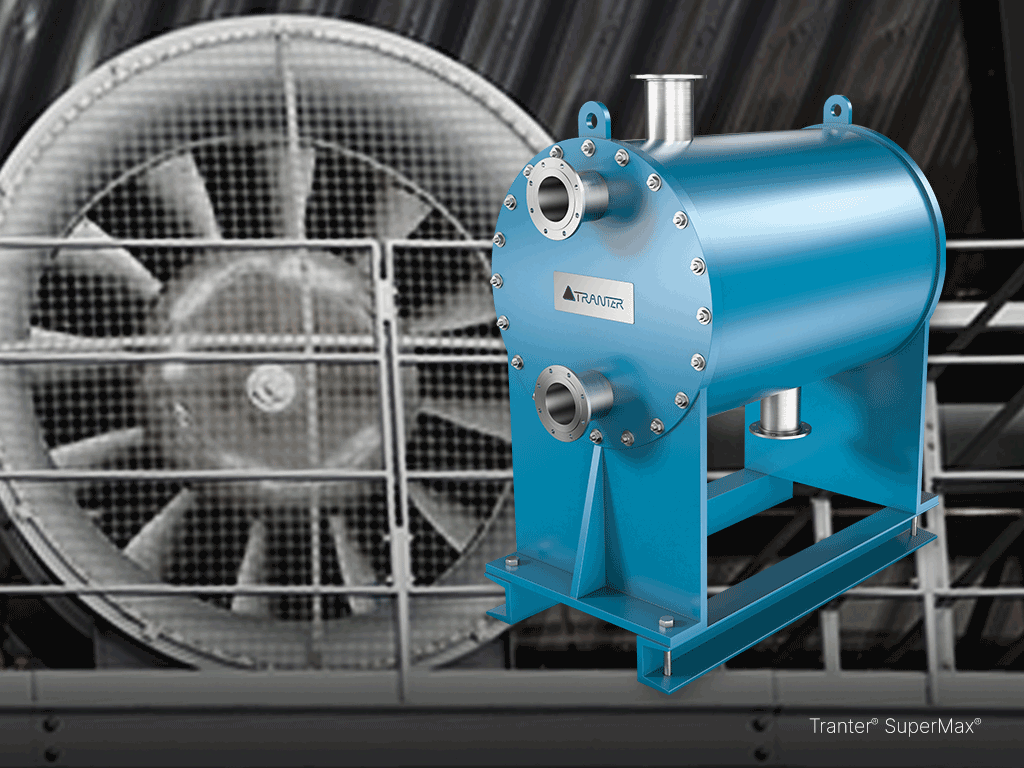
Midwest boiler manufacturer applies Supermax® shell and plate heat exchanger as a feedwater heater in a combined cycle turbine package.
Replacing traditional practice with advanced technology can be a challenging process. Sometimes, contemporary constraints can play a decisive factor in overcoming resistance. Shell and tube heat exchangers have been used as feedwater heaters since the days of Thomas Edison, and they have worked quite well. However, today’s energy needs, space constraints and globally competitive economy combine to push energy generators to higher efficiency…and new heat exchanger technologies.
Preventing corrosive condensation
In a combined cycle plant, the heat content in gas turbine exhaust generates steam, which, in turn, powers a steam turbine. The mechanical energy from both turbines generates electricity for manufacturing or to supply the electric power grid. A heat recovery steam generator (HRSG) generates steam using waste heat from the gas turbine exhaust. Its feedwater is the chemically treated, high-purity water used to drive the steam turbine. The spent low-pressure steam from the steam turbines is passed thorough a condenser to recover the water as condensate. The condensate is collected in a hot well, and then pumped back into the steam generator. The temperature at which the condensate returns to the steam generator as feedwater is critical to system maintenance and life cycle. If the feedwater entering the HRSG drum is too cold, it overcools the exhaust gases from the gas turbine. The resulting acidic condensation attacks and corrodes the boiler tubes in the HRSG.
P&F not an option
For many decades, plant operators have used S&T heat exchangers as feedwater heaters. These exchangers employ a side stream of reduced-pressure steam to heat the HRSG feedwater to a temperature that prevents corrosive condensation. Yet in today’s combined cycle plants, space is at a premium, and every cubic inch counts. Operators have considered switching to modern plate and frame (P&F) exchangers as a space-conserving solution. However, the temperature and pressure limitations of gaskets make P&F use marginal in many power generation applications, where uptime is absolutely critical. Maximum feedwater heater design conditions call for a rating of 188°C (370°F) at 36 barg (520 psig) over a wide range of cyclic operating conditions. While nominally within their capabilities, modern P&F units lack a sufficient safety factor. The required flow rates were approximately 5680 litres/min (1500 gpm) on both sides. Operators have therefore had to look elsewhere for a solution where space is critical and S&T is a last resort.
Plate efficiency with a safety factor
The boiler maker evaluated and rejected a series of welded and brazed heat exchanger types. Engineers then found that the Tranter Supermax shell and plate heat exchanger filled the need. Tranter engineering and design expertise stood out in the proof of concept stage, and qualified the company as the preferred supplier. The Supermax unit also can function as a condenser downstream of the turbine outlet. The boiler maker awarded Tranter two major orders. The units’ pressure and temperature ratings allowed for a comfortable safety factor. The evaluated first cost was competitive, and the Supermax units required 40–50% less space than the S&T exchangers. Additionally, Tranter’s engineering and project management capability became one of the major factors in the supplier selection process.
The Supermax shell and plate heat exchanger uses a low-pressure side stream to heat HRSG feedwater for finely tuned system thermal stability.
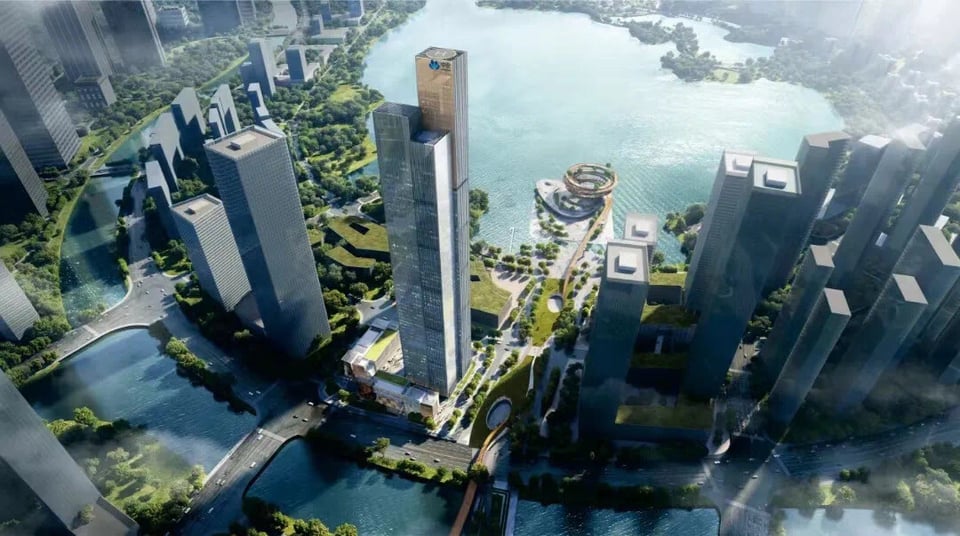
latest customer case
Tranter China joins hands with Jinmao to create a new model of sustainability
Energy, Heating and cooling