Gas dehydration with high efficiency
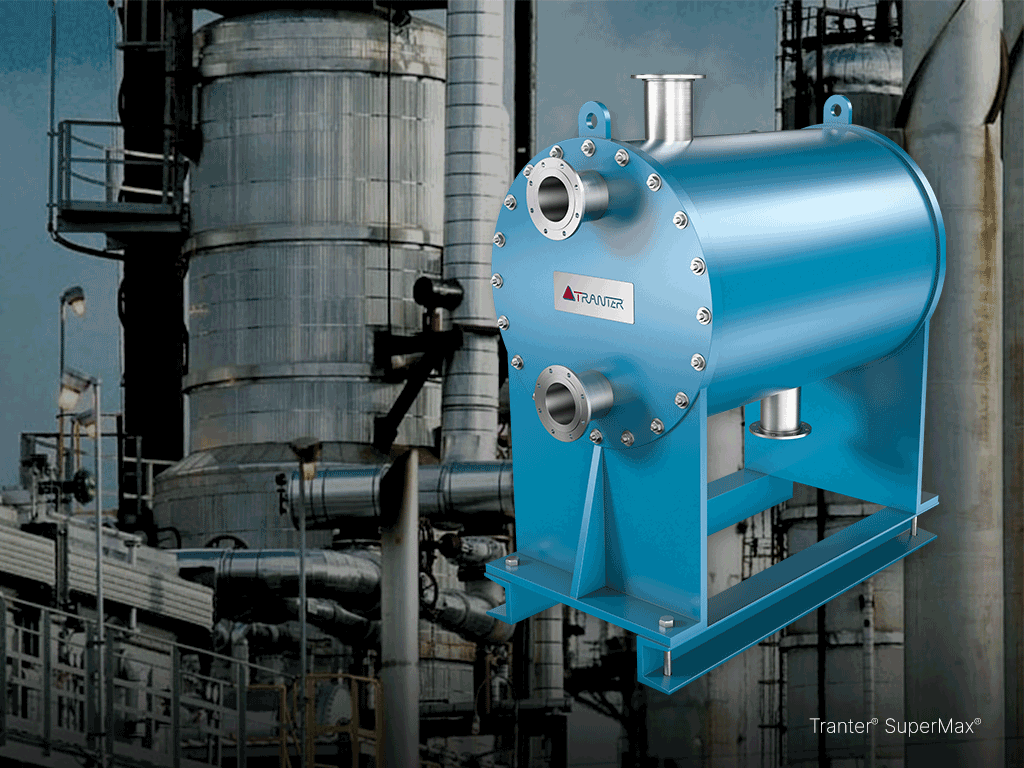
Skid maker uses two-in-one Supermax shell and plate interchangers for sustained high performance in a small footprint.
A Texas-based manufacturer of skid systems needed more efficient lean/rich TEG interchangers for its gas dehydration units. Higher efficiency interchangers would recover more heat from the hot lean TEG stream for preheating the rich TEG streams. This, in turn, would make possible a reduction in the size of the reboiler and the footprint of the skid, along with the structural complexity of the entire system. The potential savings available with higher efficiency interchangers were significant.
One interchanger provides first-stage cooling of lean TEG from the reboiler, to feed the absorber column after additional cooling. The cold-side, rich TEG stream comes from the separator, to be preheated before being fed to the reflux column for drying and stripping. The second interchanger cold-side, rich stream comes from the reflux column tube bundle, to be heated further for efficient separation.
The customer came to Tranter for a solution from within the welded plate heat exchanger product line. In addition to higher efficiency, the designers stipulated that the pressure drop across both channels must be less than 6.9 kPa (1 psi). Tranter proposed a Supermax shell and plate heat exchanger, model SM-07, in a two-in-one, multi-pass configuration for heating two cold-side, rich TEG streams in one unit.
Plates make the difference
Supermax design, construction and performance were compatible with all pressure, temperature and fluid requirements. Supermax heat exchangers are particularly suited to space constricted applications, such as skids. With their high heat transfer efficiency, they require only 30–50% of the space and up to 70% less weight compared to equivalent S&T exchangers. The unit transfers heat faster, with less fluid volume. This efficiency also means less steel, lower purchase price, shorter lead time and less expensive delivery.
Lasting efficiency
Tranter configured the Supermax unit with a three-pass/twopass, countercurrent arrangement for even, steady heating of the rich TEG. The Supermax units, subsequently furnished in several 750-, 1000- and 1500-MBTU (0.220-, 293- and 440-kW•hr sizes, fit easily within the specified footprint. Design ratings of the exchanger are 10 barg (150 psig) for the hot side and 13.5 barg (195 psig) for the cold side at 660°C (350°F), with ASME and CE stamps. The shell and cover material is SA-516- 70 carbon steel, and the plates are 0.5-mm-thick, SA-240 316L stainless steel. Selecting the Supermax exchanger has helped the integrator to reduce the size of the reboilers used in the skids. The welded unit has also resulted in a more compact skid structure with simpler support and reinforcement needs and no tube bundle pulling deadspace.
Supermax efficiency made possible reduction in the reboiler size, skid footprint and support structure.
RICH/LEAN TEG TWO-IN-ONE 1500 MBTU (440kW•hr) INTERCHANGER
FLUID DATA | ||||
Section 1, hot side |
Section 1, cold side |
Section 2, hot side |
Section 2, cold side |
|
Fluid name | Lean TEG | Rich TEG | Lean TEG | Rich TEG |
Density, kg/m3 (lb/ft3) |
0.94 | 1.04 | 1.09 | 1.08 |
Specific heat, kJ/kg•°C (Btu/lb•°F) | 3.01 (0.72) |
2.72 (0.65) |
2.43 (0.58) |
2.51 (0.60) |
Thermal conductivity, W/m•°K (Btu/h•ft•°F) |
0.12 (0.07) |
0.19 (0.11) |
0.21 (0.12) |
0.22 (0.13) |
Viscosity (avg.), cP | 1.77 | 2.33 | 5.66 | 6.35 |
PROCESS CONDITIONS | ||||
Total flow rate, kg/hr (lb/hr) | Lean TEG | Rich TEG | Lean TEG | Rich TEG |
Density, kg/m3 (lb/ft3) |
0.94 | 1.04 | 1.09 | 1.08 |
Specific heat, kJ/kg•°C (Btu/lb•°F) | 3.01 (0.72) |
2.72 (0.65) |
2.43 (0.58) |
2.51 (0.60) |
Thermal conductivity, W/m•°K (Btu/h•ft•°F) |
0.12 (0.07) |
0.19 (0.11) |
0.21 (0.12) |
0.22 (0.13) |
Viscosity (avg.), cP | 1.77 | 2.33 | 5.66 | 6.35 |
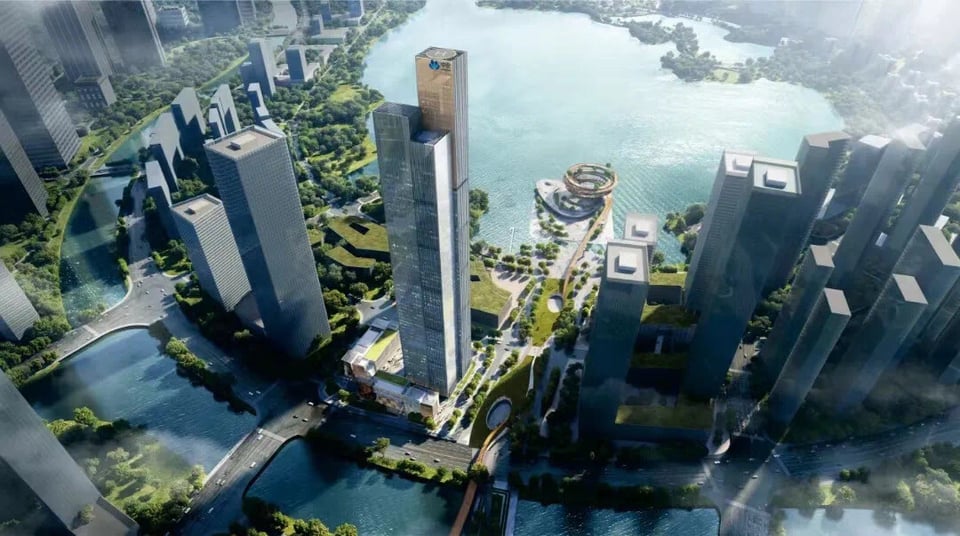
latest customer case
Tranter China joins hands with Jinmao to create a new model of sustainability
Energy, Heating and cooling