An extra measure of reliability in mission-critical compressor applications
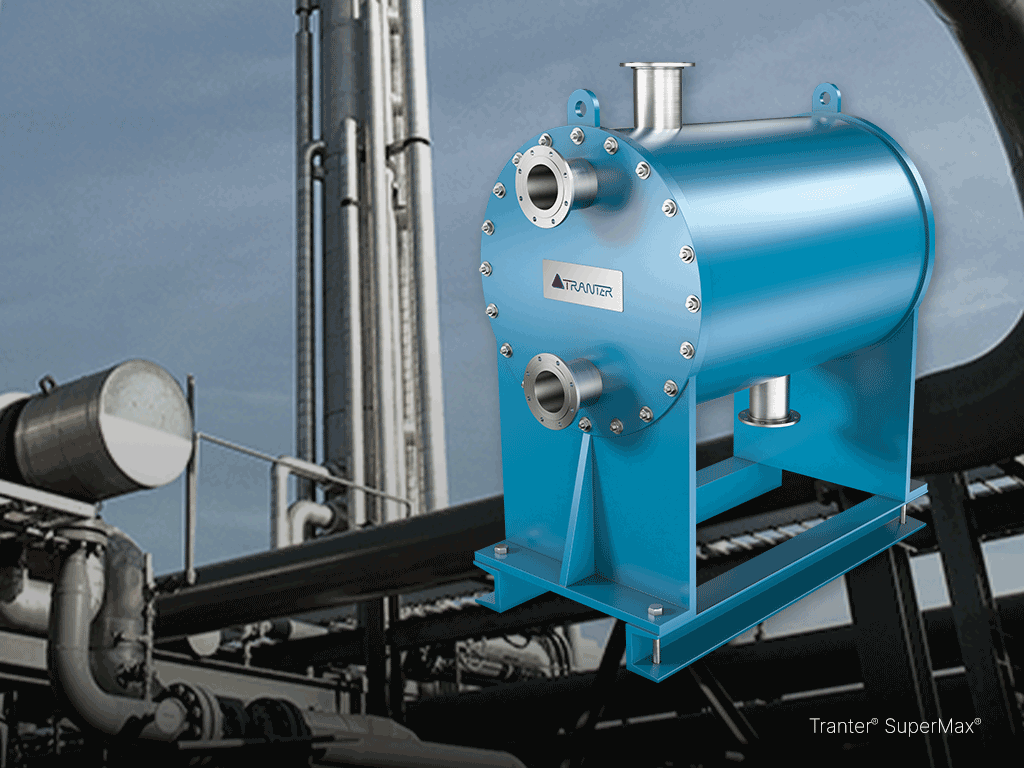
The Supermax® shell and plate heat exchanger economizes on synthetic lubricant volume and solves downtime problems caused by plate and frame heat exchanger gasket leakage
An Oklahoma-based manufacturer of packaged natural gas compression systems had been using gasketed plate and frame heat exchangers as compressor oil coolers. Despite operating pressures and temperatures being well within design limits, the manufacturer experienced gasket failures and leaking on the oil side of the exchangers, regardless of manufacturer. A plate heat exchanger solution had to be found, since shell and tube units would be too large and heavy for the skid footprint.
Oil leaks disrupt pipeline operations
These unmanned, mission-critical compression skids are a vital link in the natural gas distribution network. They are essential in keeping natural gas flowing through the network of pipelines across the country. Most are installed in isolated locations. If a compressor oil leak occurs, the entire unit shuts down when sensors detect low oil pressure or low volume in the reservoir. In addition to causing an unexpected interruption in pipeline services, a leaking skid also becomes a safety and environmental hazard. Upset conditions, such as water hammer or plugged positive displacement pump filters were thought to cause most of the gasket failures. The customer tried installing system safeguards such as pulsation dampeners and properly set relief valves to eliminate pressure spikes that could displace the gaskets. However, the gaskets were still prone to failure. The skid manufacturer evaluated a number of heat exchanger alternatives for the oil cooler application, including full surface glued gaskets, but testing showed the problem persisted with any gasketed unit evaluated.
No gaskets to fail
When made aware of the problem, Tranter proposed the Supermax shell and plate heat exchanger. Supermax design, construction and performance were compatible with all pressure, temperature and fluid requirements. With its unique design, the Supermax had no gaskets to fail. The Supermax heat exchanger is designed for pressures to 70 barg (1,015 psig) and at temperatures up to 537°C (1,000°F) for standard range units. Extended range units are available for higher temperature and pressure applications. With alternating channels for hot and cold media, the Supermax can be configured to provide true countercurrent or co-current flow. The SuperMax line offers three different diameters of circular plates.
A space-, weight-, and volume-saving solution for engineered systems
Supermax heat exchangers are particularly suited to space constricted applications, such as skids. With their high heat transfer efficiency, they require only 30–50% of the space and up to 70% less weight compared to equivalent S&T exchangers. This efficiency also means less steel, lower purchase price, shorter lead time and less expensive delivery. The unit transfers heat faster, with less fluid volume, which is a significant advantage with expensive synthetic lubricants. In the skid application, an S&T unit of the same thermal rating would require 238 liters (63 gal) of lubricant, while the Supermax would require only 87 liters (23 gal), a volume savings of 63%.
Mission-critical design
The Supermax accordion-like plate core is highly tolerant of thermal expansion. A patented compression bellows option allows for extreme thermal expansion in high temperature applications. End plates, nozzles and top and bottom covers are welded to the shell to form a pressure vessel of high integrity. Extra-large nozzle sizes can be accommodated on the shell side of the exchanger. Supermax plate materials may be Type 316L stainless steel, titanium or other alloys; shells may be fabricated of carbon steel, Types 304, 316, 316L stainless steel or titanium. The unit can be fabricated from dissimilar metals when only one side will be exposed to corrosive conditions.
A commonsense solution for short gasket life
For mission-critical applications, even where plate and frame technology meets requirements, the Supermax unit can be the commonsense answer, providing that extra measure of reliability.
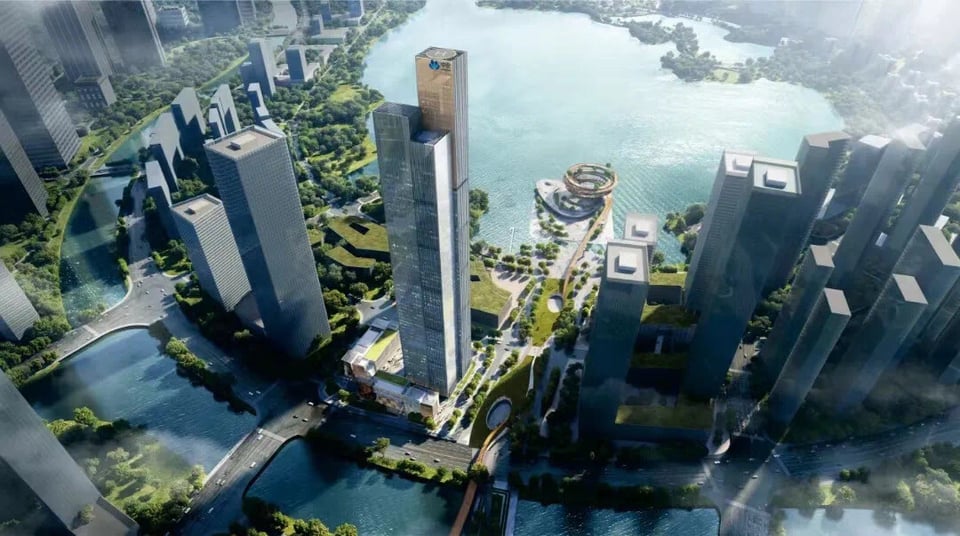
latest customer case
Tranter China joins hands with Jinmao to create a new model of sustainability
Energy, Heating and cooling