Energy, Process industries Parts and services
Why an OEM service partner for heat exchangers beats a non-OEM on any given day
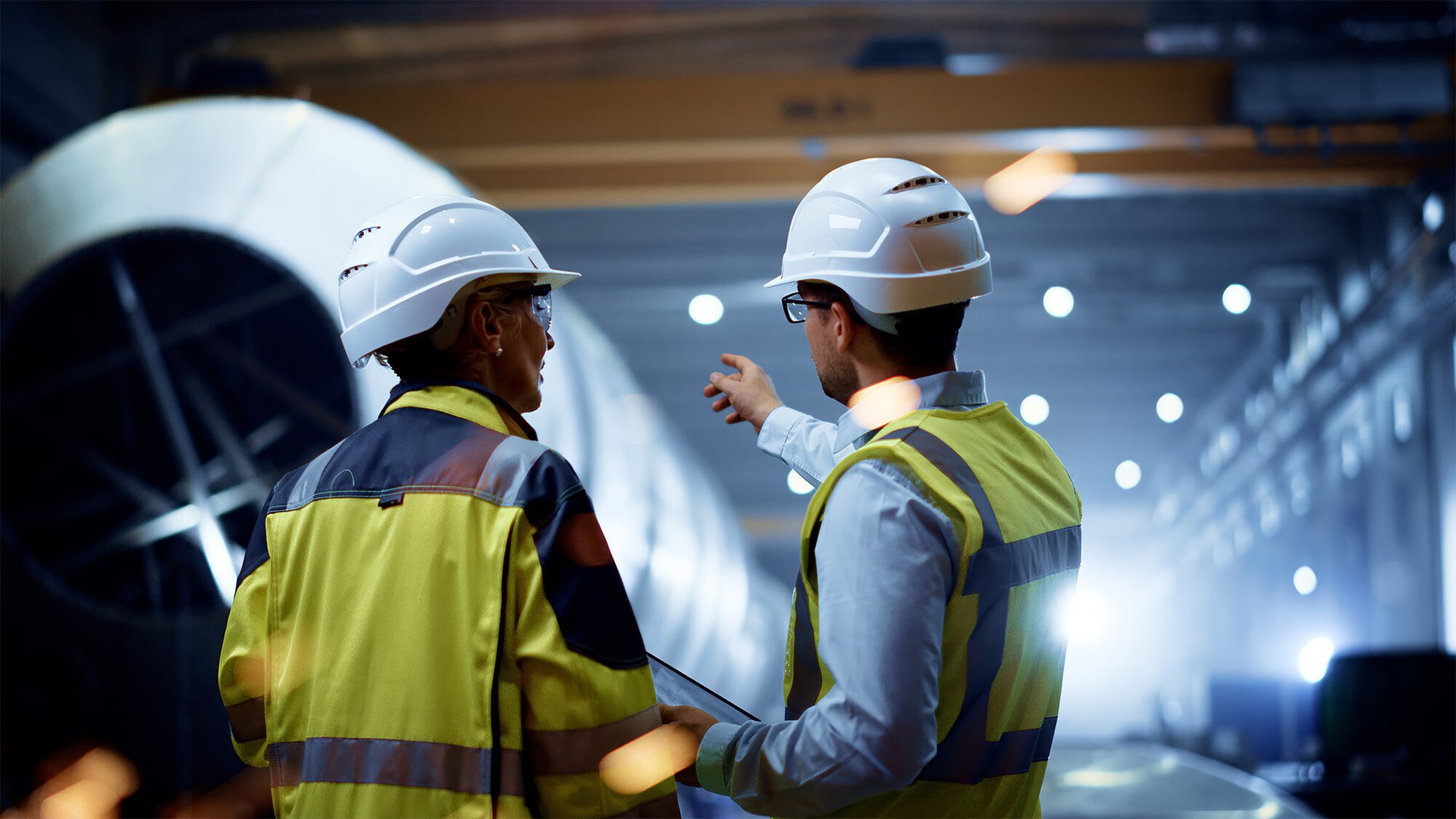
As a plant engineer, you know that choosing your heat exchanger service partner isn't just a box-ticking exercise – it's a decision that impacts every aspect of your plant's performance. But with so many factors to consider, how do you sift through the noise to find the solution that meets your needs? In this article, you’ll discover the differences between maintenance with an OEM and a non-OEM (beyond the shiny labels and sales pitches).
Breaking it down: OEMs vs. non-OEMs
Let's cut to the chase about maintaining heat exchangers. You've got two options: OEM (Original Equipment Manufacturer) or non-OEM service partners. Here’s the lowdown: Non-OEMs are usually cheaper, but there's a catch. They don’t manufacture the original equipment, so their parts might not always match up perfectly, and their stock might not be as robust. Their techs are skilled, sure, but they don’t have the knowledge that comes from years of designing and building the equipment.
On the other hand, you have OEM service providers, meaning you get service from the folks who design and build heat exchangers. They know the equipment inside and out, have the right parts on hand and have seen it all when troubleshooting. This is the deep expertise you’re paying for.
So, you need to ask yourself: Are you looking to save money now with a non-OEM or invest more in OEM services to avoid bigger headaches later?
Quick patches or perfect matches?
Is it a gamble to go for non-OEM service providers? Well, picture this: you opt for the budget-friendly choice, but what you often end up with are parts that are more about "fits most" than "fits perfectly." This route can lead to a fun cycle of wear, tear, and repairs (kind of like patching up a luxury car with duct tape). Sure, it sticks, but wouldn't you rather it be fixed correctly?
Choosing an OEM service partner, even if they aren’t the original manufacturer of your specific brand, means tapping into an unparalleled level of expertise and dedication. These experts possess blueprints, technical know-how, and a steadfast commitment to quality. What does this mean for you? Less downtime, fewer breakdowns, and not having to cross your fingers whenever you fire up your heat exchanger.
Empty cupboards or full shelves?
Have you ever checked your cupboard before grocery day? It's usually empty. That's like dealing with non-OEM service providers when you need something urgently. If something in your plant breaks down and you need a fast fix, their "We'll get it soon" could translate to unexpected and costly downtime.
Now, let's look at how OEMs play the game. Picture a well-oiled machine with parts ready to fly off the shelves at a moment's notice. Need a part? It’s already on its way, reducing wait times and the associated hair-pulling. The robust supply chain inherent to OEMs ensures that your operations continue seamlessly, without interruption.
Parts providers or problem solvers?
Let's face it: non-OEMs can be like those one-hit-wonder bands – great for a single tune but not really equipped to produce a whole album that rocks your world. They might nail it with a specific part or a particular service, but when it comes to the big picture? Not so much. They often miss the beat of offering full-service solutions that harmonize with every part of your plant's operations.
Bring in OEMs, and you’re dealing with the maestros of maintenance. These folks don’t drop off a part and call it a day; they provide various solutions tailored specifically for your operations. Want to enhance efficiency? Check. Integrate the latest tech? Done. Overhaul your maintenance program to address both the symptoms and the causes of inefficiencies? Absolutely.
It’s not me, it’s you, or it’s not you, it’s me?
Accountability is not a non-OEM’s strongest suit. When something goes wrong, it can be a merry-go-round of finger-pointing and "not my problem" attitudes (especially with those third-hand products that come without guarantees). This lack of accountability can leave you, the plant engineer, in a bind, scrambling to fix issues that no one wants to own up to.
In the OEM landscape, the approach to service is a whole different ball game. OEMs – whether they made your specific heat exchanger or not – don't just sell you a product. With support systems and warranties that would make a safety net look flimsy, they ensure any issues are noted and promptly taken care of. For them, it’s about preventing problems before they even happen – and taking full responsibility if they do.
Pay now or pay later?
Alright, let’s talk brass tacks – specifically, how OEM maintenance services actually save you money in the grand scheme of things (despite perhaps seeming pricier upfront). Imagine this: you're shopping for parts and services based solely on upfront costs, opting for the cheaper, non-OEM options. It's tempting, right? But here's the catch: non-OEMs can't match the lifecycle accuracy that OEMs bring to the table. They lack the control and insight into heat exchangers’ design and performance, making their cost predictions more of a guesstimate than an estimate.
OEMs, on the other hand, have a deep understanding of heat exchanger technology and are the bookworms of the product lifecycle. They know exactly how long heat exchangers should last in your specific applications and can pinpoint the maintenance costs you'll face down the road. This isn't just about having superior products; it's about deeply understanding those products in action.
Cover band or original artist?
Let’s say you’ve got an old car that's seen better days – a trusty old thing that’s guzzled its last gallon. You don’t want a patch-up job or a replacement part; you’re ready to upgrade to the latest model.
Non-OEMs might knock off an older OEM product through reverse engineering, but it's like getting a cover band when you could have the original artist. They can mimic the design, but capturing the improvements and innovations that come with genuine OEM products? That’s usually out of their league. They lack original research and development insight, which means they can get close, but they don’t quite hit the mark.
Enter OEMs. When you reach out to them, it’s not about replacing the old with the same old. OEMs continuously innovate, offering you not just any replacement but an improved version of what you have. These are upgraded, optimized, and fine-tuned to enhance performance, reduce costs, and improve efficiency in ways that simply weren't possible 15 years ago.
One-stop-shop or single service provider?
If the original manufacturer of your heat exchanger is no longer around or isn't meeting your service expectations, don't think you have to settle for less. We at Tranter extend the OEM advantage to non-Tranter heat exchangers too. In fact, we service every brand on the market. Whether it’s providing parts, service, or operational advice, we ensure you don't miss out on any benefits of working with a seasoned OEM – no matter what.
And if your facility operates a variety of heat exchanger brands, imagine the simplicity and efficiency of dealing with a single, reliable service provider. Tranter can be that one-stop-shop, bringing consistency, expertise, and a proactive service approach to every type of heat exchanger under your roof.
Excited by the prospect of streamlining your heat exchanger maintenance with a one-stop solution like Tranter? In our guide, "Tranter’s multi-brand heat exchanger service (and why it's a game-changer for your plant)”, we unpack how our savvy, all-encompassing service transforms maintenance strategies – offering you unparalleled flexibility and efficiency across various applications.