Sick of not getting quality parts in time? Tap into our global supply chain and end the hassle
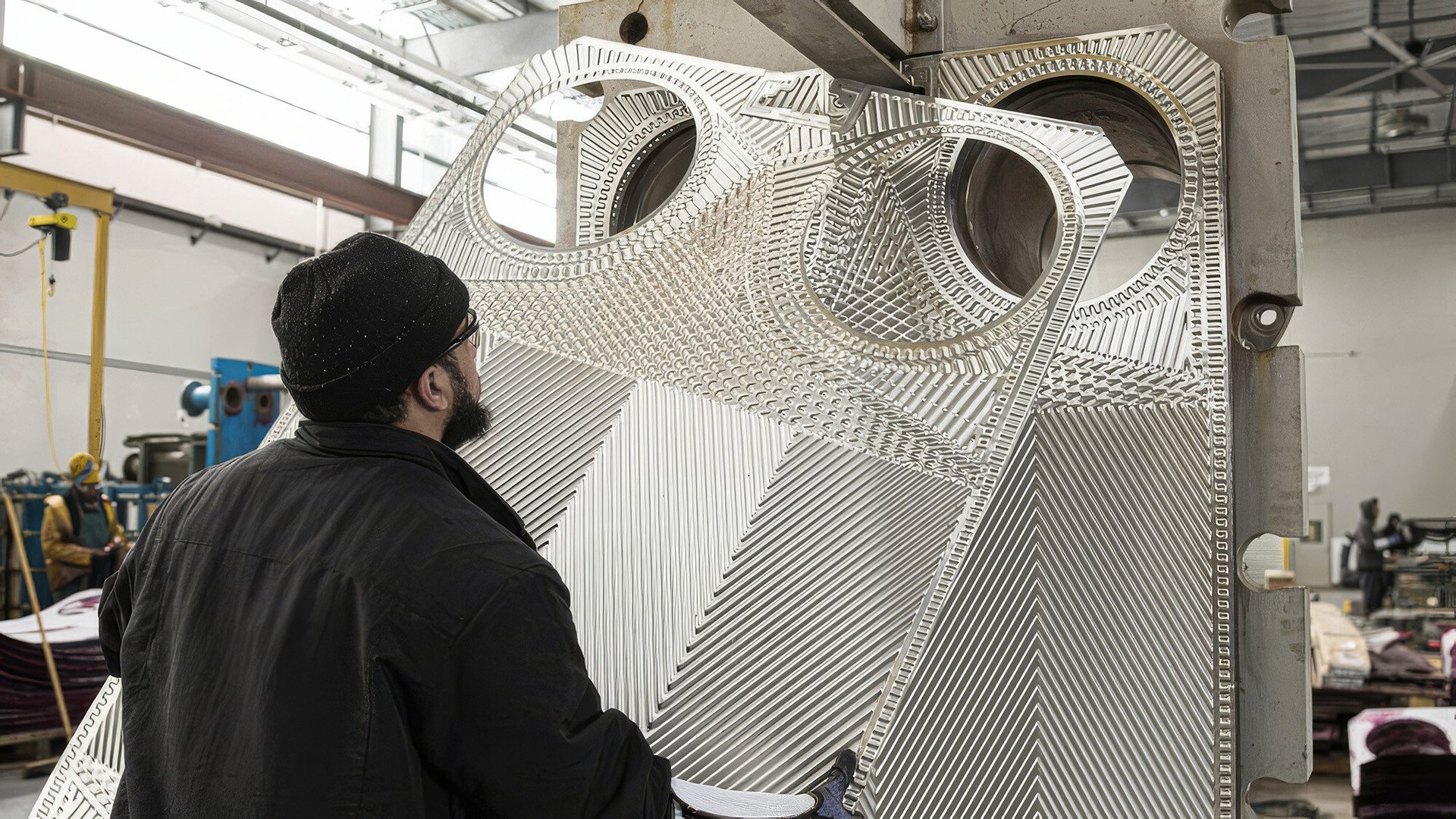
Ever feel like you’re playing a never-ending game of catch-up to get the heat exchanger parts you need? You’re not alone. Plant engineers everywhere are fed up with constant delays, inconsistent quality, and the logistical nightmares of managing multiple suppliers. You’ve got a plant to run, and time is your worst enemy. In this article, you’ll dive into common issues that trip you up and learn how Tranter’s solutions transform your plant into a powerhouse of efficiency and reliability.
No more production delays and logistics challenges
Let's be real – waiting two months for critical heat exchanger parts is unacceptable. The lengthy production process, compounded by logistics hurdles, can throw your entire schedule into chaos. You’ve got parts from overseas, hard-to-get raw materials, and the complex dance of production scheduling. It’s a headache.
But at Tranter, we’ve got your back. We don’t just wait for problems to arise; we anticipate them. By keeping a strategic stockpile of essential raw materials, we drastically cut down your wait time. Need parts with strict country-of-origin requirements? We’ve got them on the shelf, ready to go. Our proactive approach means we can kick off production the moment you need it. We’ve also nailed down rock-solid terms with our suppliers, so components like gaskets are already in the U.S., meaning, no more waiting for months.
Beating the air freight blues
We get it. Air freight is a wallet-buster. Sure, it's fast, but it's also a budget nightmare. Add in the rigid constraints of production scheduling, and you’re staring down the barrel of prolonged downtime and skyrocketing costs while you wait for those critical parts.
Enter Tranter. We’ve got a smarter, more cost-effective solution. Even if a part isn't available at your local site, it’s likely in stock elsewhere in our network. We can shuffle inventory around the globe to fulfill your order fast without resorting to pricey air freight. This savvy approach slashes wait times and saves money, keeping your operations humming without breaking the bank.
Taming the chaos of variable components
Dealing with heat exchanger components from different regions can be a real headache. Parts variability not only complicates sourcing but can also lead to quality inconsistencies and frustrating downtimes as you wait for the right piece to arrive.
Tranter thinks differently. We’ve standardized our heat exchanger components across all regions. This means you get uniform parts that are easy to source and consistently high in quality, no matter where you are. With Tranter, you’re always covered with top-notch components.
Crushing quality control discrepancies
Juggling multiple suppliers for heat exchanger parts is a recipe for disaster. Tiny variations in manufacturing, like plate thickness, can wreak havoc on thermal dynamics. And when you’re dealing with hundreds of plates, these minor differences add up to major performance headaches.
Tranter cuts through this chaos with our single-source solution. We’ve got the industry smarts and rigorous quality standards to ensure consistent quality across all components. No more discrepancies. No more performance issues. Just reliable, top-quality parts every time. In other words, you get the peace of mind that comes from knowing every part is up to the highest standards.
Tackling performance inconsistencies
On that note, mixing and matching parts from various suppliers in refurbished units can spell trouble. When components don’t play nice together, you’re left with inefficiencies and unexpected downtime – a nightmare for any plant engineer.
We got you covered with a holistic approach to maintenance and refurbishment. Tranter ensures that every part we use is compatible and works in perfect harmony. Our flexibility in sourcing means we can creatively solve problems, even pulling in components from outside our brand when needed. This guarantees that your refurbished units perform at their best, giving you reliable, efficient operations without the guesswork.
Conquering scattered delivery times
Playing the waiting game with multiple suppliers is a logistical nightmare. One part arrives in a week, another in four, and suddenly, your maintenance schedule is in shambles. These inconsistent delivery times cause chaos in your planning and keep your operations in constant delay.
We at Tranter simplify your life by being your single point of contact. We coordinate the sourcing and delivery of all your parts through our global network. Our reliable logistics ensure that all components arrive together, cutting down wait times and making your planning process a breeze.
Destroying inefficient demand forecasting
Nailing demand forecasting is no easy feat. When a supplier gets it wrong, they either end up drowning in excess inventory or scrambling to fill orders – both of which hit your bottom line hard. Throw in some departmental misalignment, and you’ve got a recipe for chaos and inefficiency.
Tranter smooths out these wrinkles by synchronizing demand forecasts across all departments. We dive deep into sales projections and historical data to pinpoint the perfect safety stock levels. By aligning on a unified plan for North America, we ensure our inventory system is always up-to-date and orders are processed faster. This coordinated strategy means you get the parts you need right when needed.
Overcoming limited flexibility in meeting customer demands
Rigid supply chains and inflexible inventory strategies can leave you high and dry when customer demands fluctuate. When suppliers can't adapt quickly, this can lead to dissatisfaction and even cost you business.
That's why we flip the script with unmatched flexibility. Tranter constantly align our operations to meet your changing needs. By maintaining a dynamic approach to inventory and supply chain management, we stay ahead of the curve. This adaptability means we respond swiftly and efficiently to your requirements, consistently exceeding expectations and delivering top-notch service every time.
Eliminating gaps with comprehensive regional coverage
A one-size-fits-all strategy just doesn’t cut it when it comes to regional demands. Overlooking specific needs in different areas can lead to service gaps, delays, and unmet expectations, frustrating you and your customers.
Tranter takes a more innovative approach by aligning our strategies to cater to regional specifics. We dive into each area's unique demands and maintain safety stock levels accordingly. This targeted alignment ensures that every region is covered comprehensively. By doing so, we boost our responsiveness and guarantee that the necessary stock is always on hand to meet regional demands effectively.
You've seen how Tranter’s global supply chain can transform your plant's operations from chaotic to seamless. Now, it's time to take the next step. Our in-depth guide, "Tranter’s multifaceted heat exchanger service (and why it's a game-changer for your plant)", is packed with insights and strategies to help you leverage our services to their fullest potential. Download it today and discover how Tranter can revolutionize your plant’s efficiency and reliability!