Energy, Heating and cooling Parts and services Marine and shipbuilding HVAC Heating & Cooling
How to choose the ideal heat exchanger type for your application
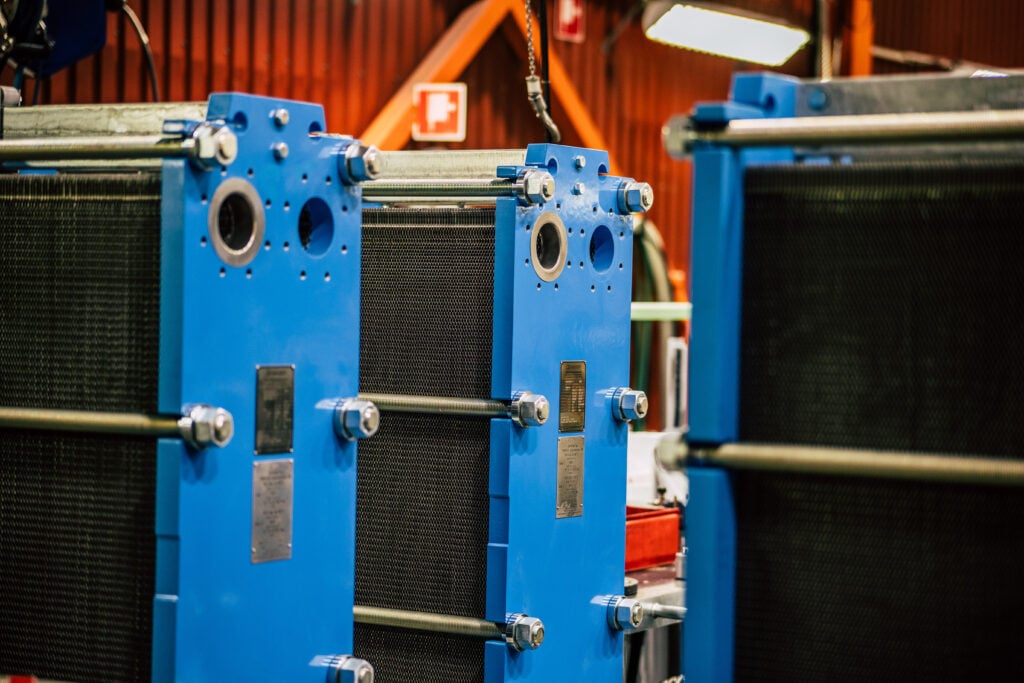
Looking for the ideal heat exchanger for your application? Learn how to choose the right type of heat exchanger for your needs with this comprehensive guide.
_________
There are several factors you need to take into account when selecting a heat exchanger for your application. It’s important to carefully consider each limitation you face in order to ensure the best performance and return on investment. By selecting a model that is well-suited to the specific application and operational conditions, you can help to maximize efficiency and minimize potential problems or failures. But with many different heat exchangers available, how can you determine which one is the best fit for your needs?
The bottom line is to aim for the best-intended performance of your heat exchanger. Every application has its own unique requirements. To achieve the best possible performance in your specific application, you need to consider a variety of factors:
- Pressure drop
- Available space for installation
- Floorage
- Maintenance requirements
- Installation costs
- The type of equipment most suitable for your needs
Selecting the wrong heat exchanger or design can result in inadequate cooling or heating, or fouling, which can cause significant maintenance requirements and lead to a loss of time, money, manpower, and productivity. Therefore, it’s essential to have a thorough understanding of your processes and requirements when choosing the appropriate equipment.
And while some types of heat exchangers have been widely used for many years, new technologies are now available that can provide better performance, save space, and reduce long-term costs. It’s important to understand the advantages that new technologies can offer over traditional heat exchangers and to evaluate all available options before making a final decision.
The three types of heat exchangers (and what they’re good for)
There are three types of commonly used heat exchangers – all for different purposes. Each one has unique features that make it suitable for specific applications and operating conditions. The three types of heat exchangers are:
1. The gasketed plate heat exchanger (GPHE)
The gasketed plate heat exchanger uses metal plates with corrugated surfaces to transfer heat between two fluids, which flow through alternate channels and are separated by the plates. This type of heat exchanger is a versatile option you can use in a wide range of applications where there’s a need for both cooling and heating, as long as the temperature and pressure are within reasonable limits. They can handle temperatures up to 350 degrees Fahrenheit and pressures up to 370 psi, but they should not be used in high-temperature, high-pressure applications, as this leads to a shorter gasket life.
You can apply GPHEs in various industries, such as chemical, petrochemical, oil and gas, acid cooling, and battery services. However, the compatibility of the heat transfer medium with the gaskets depends on the specific process parameters. The gaskets are also the Achilles heel of the GPHE, as exceeding the recommended pressure and temperature limits can cause gasket failure. Use this chart to help determine which fluids are compatible with the gaskets.
GPHEs fit well within certain boundaries and are designed with modularity and flexibility in mind. This means you can open them, add or remove plates, and clean them individually – making maintenance relatively easy. The modular design also means you can replace gaskets when needed. Overall, the GPHE offers a flexible and efficient option for a variety of heating and cooling needs, with the added advantage of easy maintenance and the ability to adapt to changing process conditions.
2. The block heat exchanger (BHE)
The block heat exchanger offers a middle ground between the gasketed plate heat exchanger and the shell and tube heat exchanger (see #3). It’s designed with ease of maintenance in mind and consists of four panels that you can easily unbolt and wash for cleaning. You can also remove and clean two of the panels if only one side is dirty, making it highly flexible. It can accommodate up to 20 plates and handle complex duties with a small temperature approach and footprint. The block heat exchanger can handle pressures up to 600 psi and temperatures up to 700 Fahrenheit.
Block heat exchangers are particularly popular in refineries due to their regular maintenance needs and small footprint with an effective heat transfer area. They are mostly used in enrichment services (part of the oil and gas process). But, as refineries require higher temperatures and pressure, they need to be cleaned more often. Therefore, block heat exchangers are preferred over shell and plate heat exchangers, which take up to 5-6 times the space.
In addition to their space-saving benefits, block heat exchangers can also handle larger flow rates in flow applications. This means that they are often used in situations where two shell and tube heat exchangers would be required to match the capacity of a single block heat exchanger. However, it’s important to note that the design and performance of a block heat exchanger will vary depending on your specific application, so it’s important to carefully consider the process parameters and requirements before selecting this type of heat exchanger.
3. Shell and plate heat exchanger (SPHE)
The shell and plate heat exchanger (SPHE) is a hybrid between the shell and tube and plate heat exchangers. When considering a shell and plate heat exchanger (HE) for your application, it’s essential to understand its unique design and capabilities.
Shell and plate HEs are constructed with a round cylinder and plates that are round and welded without gaskets. This design enables them to withstand high temperatures and pressures, making them an ideal choice for high-pressure and high-temperature applications. They can handle up to 1000 Fahrenheit and 1450 psi, which is similar to their big brother, the shell and tube HE, which can handle even higher temperatures and pressure. This feature also makes the SPHE more durable and resistant to fouling and corrosion than gasketed plate heat exchangers.
However, it’s worth noting that cleaning an SPHE can be challenging and requires special attention. The circular design of the shell makes it difficult for you to access the plates, resulting in maintenance and cleaning being more complex. While they are commonly used in steam and gas applications, they may not be the best fit for all applications. That’s why, when considering an SPHE, it’s crucial to consider the specific requirements of your application.
PRO TIP:In some cases, there may be an overlap between Shell and Tube and BHE capabilities. If your temperature and pressure requirements are suitable for both, block heat exchangers can be a more optimized solution. BHEs offer up to 20 passes, which means better customization and increased heat transfer efficiency. |
What to keep in mind
In summary, when choosing your heat exchanger, you need to consider factors such as performance, maintenance, cost, pressure drop, and working fluid to get the best results. By calculating the right design and parameters for your application before selecting a heat exchanger, you ensure optimal performance, reduce maintenance costs, and improve overall productivity.
Interested in knowing more about heat exchangers or finding out which one suits you best? Whatever your needs are, we help you make an informed decision. We can also assist you with installing, maintaining, and repairing your heat exchanger to ensure it performs optimally throughout its lifespan. Contact us now to schedule a consultation with one of our experts.