Energy, Process industries Energy, Heating and cooling
How advanced thermal hydraulics solve your process efficiency challenges
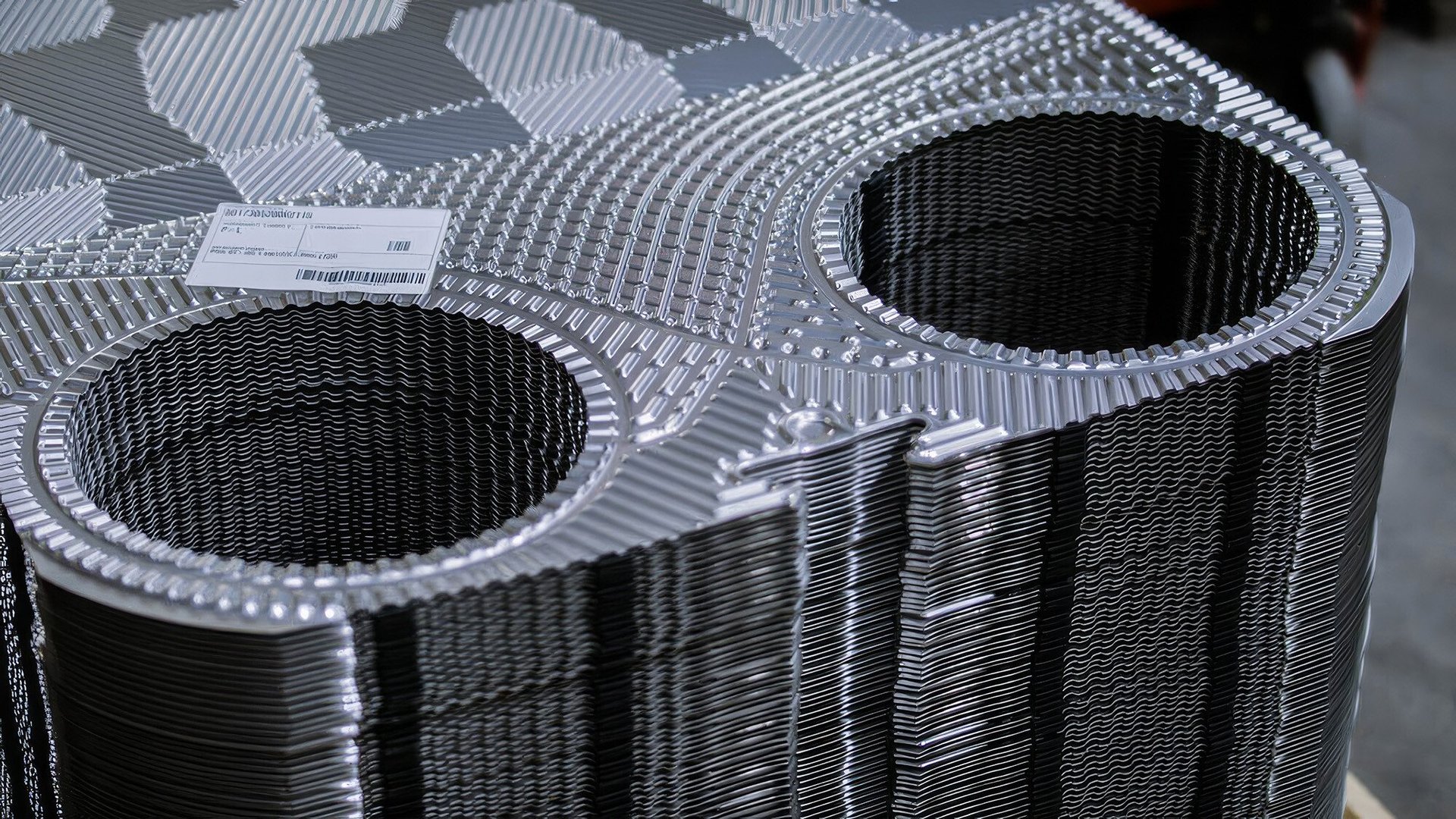
Ever wonder why some heat exchangers are better than others? It’s all about thermal hydraulics performance. Here, you’ll explore how advancements in the technology are revolutionizing heat exchanger performance, boosting process efficiency, and cutting long-term costs.
What is thermal hydraulic performance?
Here’s the breakdown: Thermal and hydraulic performance aren’t isolated aspects of heat exchanger operation – they work together to drive process efficiency. Think of it this way: thermal performance focuses on how effectively your heat exchanger transfers heat between fluids, while hydraulic performance ensures that the fluids move optimally within the system with minimum pressure drop.
By balancing these two types of performance, you’ll achieve what's known as thermal hydraulics. This balance is crucial because an efficient heat exchanger needs both effective heat transfer and smooth fluid dynamics. If either aspect is off, you’ll face issues like inefficient energy use, increased operational costs – or even equipment failure.
Key components of heat exchanger thermal performance
Understanding thermal performance in heat exchangers means focusing on how efficiently heat is transferred between fluids. This aspect of performance is crucial for maximizing energy output and ensuring your processes run smoothly. These are the key components that make up thermal performance (Q= U*A*LMTD):
- Surface area (A):
Think of the surface area as the battleground where fluid A and fluid B (like air and water) meet. The more surface area you have, the better the heat exchange. It's a simple concept with huge implications for efficiency.
Bonus tip: We at Tranter have designed a new OmniFlex™ corrugated pattern to increase surface area and hence increase thermal performance.
- Temperature difference: (LMTD, Driving force of heat transfer)
The magic happens with temperature difference. This is typically specified by both you and your customer. Imagine an engine running at 300°F that needs to cool down to 100°F. That's where the heat exchanger comes in, controlling that temperature drop to keep everything running smoothly.
- Thermal conductivity (U):
When it comes to heat transfer, it's all about the overall heat transfer coefficient (U). This coefficient accounts for the flow resistance, which is influenced by both fluid and metal properties.
It includes factors like the thermal conductivity (K) of the material, the heat transfer coefficient (H), and the impact of fouling. Together, these elements ensure that while the fluids remain separated, efficient heat transfer still takes place across the exchanger.
Hydraulic performance factors
Hydraulic performance, on the other hand, deals with the movement and behavior of fluids within the heat exchanger. It’s essential for maintaining stable and efficient operations by managing flow rates, distribution, and pressure drops. Here are the key factors influencing hydraulic performance:
- Fluid dynamics:
Hydraulic performance translates into how the fluids move within the heat exchanger. We're talking temperature, fluid type, and direction. You might have counter flow, cross flow, or even advanced configurations like barrel flow in the latest designs like the Novusbloc® welded block heat exchanger.
- Flow rate and distribution Area:
Flow rate and distribution are your best allies in maximizing efficiency. They directly impact how smoothly and effectively heat is transferred within your system.
But here’s where it gets even better – Tranter’s R&D team takes it up a notch. By using advanced simulations and fluid flow analysis, we optimize the design of the distribution area to ensure your heat exchanger performs at its best.
- Pressure drop
Keep an eye on the pressure drop. Too much, and you lose operational efficiency. Too little, and you might not be transferring heat effectively. It's all about finding that sweet spot to prevent fouling and maintain peak performance.
Thermal hydraulic performance in heat exchangers = improved process efficiency
- Power and energy optimization
Let’s get straight to the heart of why thermal hydraulic performance in heat exchangers is a big deal for your process. The primary goal of using plate heat exchangers (PHE) is to maximize power output – measured in kilowatts per hour (KW/H).
The more power you can extract, the better your process efficiency. By optimizing heat exchanger design, you can significantly boost the amount of energy transferred, either saving energy or adding it to the system. This is key to achieving higher efficiency in your operations.
- Reducing energy consumption
Efficiency is more than just maximizing power; it's also about minimizing waste. An optimized heat exchanger design drastically reduces energy consumption.
By enhancing thermal hydraulic performance, you ensure that the heat exchanger operates more efficiently, consuming less energy while delivering the same or even better results. This dual benefit of energy savings and improved output is why thermal performance is critical for your process.
- Stable and efficient operations
Advanced thermal hydraulic performance contributes to a more stable and efficient process. By achieving low fouling and optimal turbulence, your heat exchangers maintain stability in operation.
This stability is crucial because it ensures consistent performance, reducing the risk of sudden failures or inefficiencies. A stable system is easier to operate and maintain, leading to smoother, more reliable operations overall.
- Pressure drop management
Managing pressure drop is crucial for maintaining system efficiency. In a heat exchanger, pressure drop refers to the loss of pressure as fluids move through the system. Too much pressure drop can restrict fluid flow, leading to inefficiencies and higher energy consumption. On the other hand, too little pressure drop might indicate poor heat transfer.
Optimized heat exchangers are designed to strike the right balance. By controlling the pressure drop, you maintain a steady flow and ensure consistent heat transfer. This balance is key to keeping your system running smoothly.
- Competitive advantage
Improving thermal hydraulics in heat exchangers also makes your equipment more competitive. In a market where efficiency and innovation are key differentiators, having high-performance heat exchangers sets you apart.
Customers are looking for solutions that not only meet their needs but also offer additional benefits like cost savings and energy efficiency. By applying advanced thermal hydraulic performance, you position your equipment as the superior choice, leading to better market competitiveness.
- Long-term energy optimization
Finally, advancements in thermal hydraulics contribute to long-term energy optimization. A well-designed heat exchanger doesn't just perform better initially; it maintains its efficiency over time.
Longevity means sustained energy savings and cost reductions throughout the lifespan of the equipment. Investing in advanced thermal hydraulics is an investment in the future efficiency and cost-effectiveness of your processes.
Tranter’s advancements in thermal hydraulics
Tranter’s advancements in thermal hydraulics come from over 90 years of hands-on experience and cutting-edge R&D. We've learned what works – and more importantly, what works best. Here’s how we’ve pushed the envelope to boost your heat exchanger performance.
- Enhanced plate design and turbulence
Plate design and turbulence are two game-changers in heat exchanger performance. By tweaking the plate design and adding corrugations, we crank up the turbulence inside the heat exchanger.
The result? Enhanced heat transfer performance. More turbulence means better mixing of the fluids, which translates to more efficient heat transfer. Think of it as creating the perfect storm inside your heat exchanger to maximize efficiency.
Tranter’s THERMOFIT™ Plate SeriesTranter’s latest innovation, the THERMOFIT™ Plate Series, featuring the patented Omniflex™ plate pattern, is a game-changer in heat exchanger design. This advanced plate pattern maximizes energy efficiency by inducing high turbulence, which boosts heat transfer rates while maintaining a low-pressure drop. Not only does this improve thermal performance, but it also minimizes plate deformation and reduces flow stagnation. The tool draw depth varies to minimize the spring-back effect. Here’s a quick breakdown of what makes this design so effective:
|
- Advanced gasket design
Now, let’s dive into gaskets. For us, they’re not just about sealing; they’re about sealing reliably. Advanced gasket designs ensure no leaks, which is crucial for maintaining pressure ratings and overall efficiency.
A well-designed gasket keeps everything contained, allowing your optimized plate design to do its job. No leaks mean no pressure drops, and that means better performance all around.
Tranter, gaskets, and FEATranter uses advanced finite element analysis (FEA) to perfect gasket sealing, ensuring higher pressure ratings and superior reliability. This precision design process optimizes the gasket’s performance under real-world conditions, making sure your system stays leak-free and efficient. Key benefits include:
|
- Minimizing fouling
Fouling is the bane of a heat exchanger’s existence, right? But recent innovations are tackling this head-on. By designing heat exchangers to minimize stagnant flow and increase turbulence, we’re significantly reducing fouling. This keeps your heat exchanger running cleaner for longer, improving efficiency and lifespan. Less fouling means less downtime and more reliable performance. - Material innovations
Material choice is another critical factor. Advances in material science have brought us new options that improve heat transfer and resist corrosion and fouling. The right materials make all the difference.
We’re constantly researching and integrating new material technologies to push the envelope on performance and durability. Using top-notch materials ensures your heat exchanger operates at peak efficiency, even under tough conditions.
TRANTER INSIGHT:Tranter’s R&D team stays ahead by constantly monitoring the latest advancements in elastomeric materials, ensuring we deliver sealing technology that’s safe, cost-effective, and state-of-the-art. By rigorously testing gasket materials to meet engineering standards and collaborating with leading elastomer vendors, Tranter’s product development team handpicks the best material for each specific application. That way, you're always getting a solution that’s perfectly suited to your operational needs. |
- Smart technology integration
Let’s not forget smart technology. IoT (Internet of Things) is revolutionizing how one monitors and maintains heat exchangers. With real-time data and predictive analytics, you can stay ahead of maintenance needs and optimize performance on the fly.
Smart systems mean fewer surprises and more control over your operations. And this tech isn’t the future – it’s the present. Integrating these systems makes your heat exchangers smarter, more efficient, and more reliable.
Optimizing the thermal hydraulic performance of your heat exchangers is one of the things you can do to boost process efficiency and cut costs. Want to take it one step further? Tranter's 90+ years of innovation have led to some of the most advanced solutions in the industry – discover how.