Parts and services Marine and shipbuilding
Hidden costs in vessel management: How your heat exchangers impact your bottom line
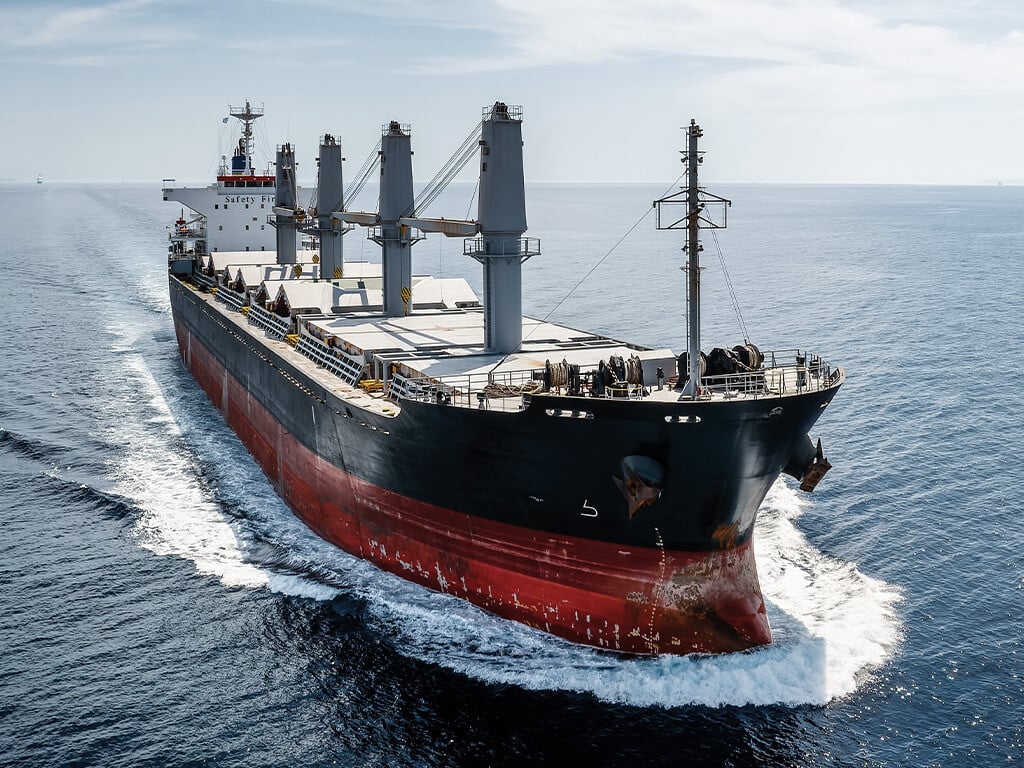
Managing vessels is no easy task, and as a vessel manager, you’re already navigating tight budgets, strict schedules, and high-pressure operations. But one overlooked component can significantly disrupt your plans: heat exchangers. These systems play a crucial role in your vessel’s performance, and when they’re not properly maintained, hidden costs start to pile up faster than you’d expect. Here, you’ll learn how they affect your bottom line.
The domino effect of neglecting heat exchanger maintenance
A seemingly minor issue like an aging gasket can escalate into a major crisis. Take this example: old gaskets on an oil cooler begin to harden and crack, causing a leak of 100 liters of oil per hour. Suddenly, you’re dealing with operational stoppages, fire hazards, and safety authorities barring the vessel from continuing its journey. If spare parts aren’t on board, your team is forced to improvise – incurring costs for expedited shipping, technician travel, and extended downtime.
Let’s break the example down:
- Air freight for parts: €20,000
- Technician travel and labor: €15,000
- Dry dock penalties: €50,000–100,000 per day
What could have been a manageable maintenance task balloons into a financial and logistical nightmare. In other words, it pays to be proactive, don’t you think?
Performance inefficiencies: the hidden ripples
Even when heat exchangers are operational, inefficiencies can drain your resources. and often go unnoticed. Small performance dips, like reduced cooling or heating, may seem insignificant at first but gradually impact overall operations, increasing fuel consumption and extending crew hours without raising immediate alarms.
Reduced cooling or heating performance slows the vessel, increasing fuel consumption and prolonging crew hours. Delayed container deliveries lead to penalties from freight customers, further compounding the issue.
Another example is freshwater generators reliant on heat exchangers. When these fail, you’re forced to bunker freshwater at every port – a costly workaround that adds up over time.
Why inefficiencies happen
Vessel operations are dynamic, and maintenance often takes a back seat. Here’s why:
- Rotating crews: Frequent changes in personnel create gaps in maintenance knowledge.
- Budget pressures: Maintenance activities are often deferred to avoid exceeding allocated budgets.
- Limited tracking systems: Many vessels lack a unified system to document maintenance history, leaving managers in the dark about past or upcoming needs.
The result? Maintenance is pushed to dry dock windows or ignored entirely, increasing the risk of sudden failures and escalating costs.
Choosing the wrong partner amplifies costs
Partnering with the wrong supplier can wreak havoc on your operations. Low-quality heat exchangers might look like a bargain upfront, but the hidden costs will hit you hard down the line:
- Frequent breakdowns: Cheap parts fail faster, leaving you scrambling to schedule emergency repairs that derail operations.
- Subpar performance: Inferior heat exchangers don’t just underperform—they compromise critical systems, like fuel preheaters or freshwater generators, risking larger operational setbacks.
- Extended delays: Downtime due to unreliable equipment and slow fixes translates to penalties, missed schedules, and ballooning costs.
And it’s not just the equipment. Suppliers who overpromise and underdeliver – whether through missed deadlines, incomplete info, or broken commitments – add chaos to your already packed plate. These mistakes cost you time, trust, and operational control, and eventually, money.
Here’s the truth: in a high-stakes environment like yours, supplier reliability is non-negotiable. When you work with a trusted partner, you’re investing in smoother operations, stronger safety, and a bottom line that doesn’t bleed cash due to avoidable errors.
Real-world example: a costly lesson in neglect
Picture this: An LT cooler gasket on a vessel goes unnoticed during routine checks. Eventually, it starts leaking, costing up to €7,000 in immediate material losses. The unplanned repair triggers a cascade of additional costs:
- Parts air-freighted to Brazil: €20,000
- Technicians flown in: €15,000
- Non-stop work schedules on board: €5,000
Before long, the vessel’s journey is delayed, penalties mount, and the total expense gets close to €50,000. All of this could have been avoided with timely maintenance and a reliable heat exchanger partner.
Solutions to avoid hidden costs
Feeling overwhelmed by these costs? Don’t worry, here’s the good news. Hidden costs can be minimized with a proactive approach:
- Stick to a maintenance schedule: Regular servicing reduces the risk of sudden failures. For example, replacing gaskets at the right intervals costs just €500 compared to €4,000 for emergency replacements.
- Implement a tracking system: Record and monitor maintenance history to ensure every component is inspected and serviced on time.
- Partner with reliable experts: Work with trusted providers like Tranter, whose OEM-quality products and global network ensure efficient, cost-effective solutions.
Your heat exchangers might not be the first thing on your mind, but ignoring them will cost you – and your bottom line – in the long run. By addressing inefficiencies and partnering with the right experts, you can keep your vessel running smoothly and cost-effectively. But how does one do that, exactly? Read our article, “Streamline your vessel's heat exchanger maintenance with a multi-brand service provider” to find out.