Heat exchanger applications: types, industries & how they work
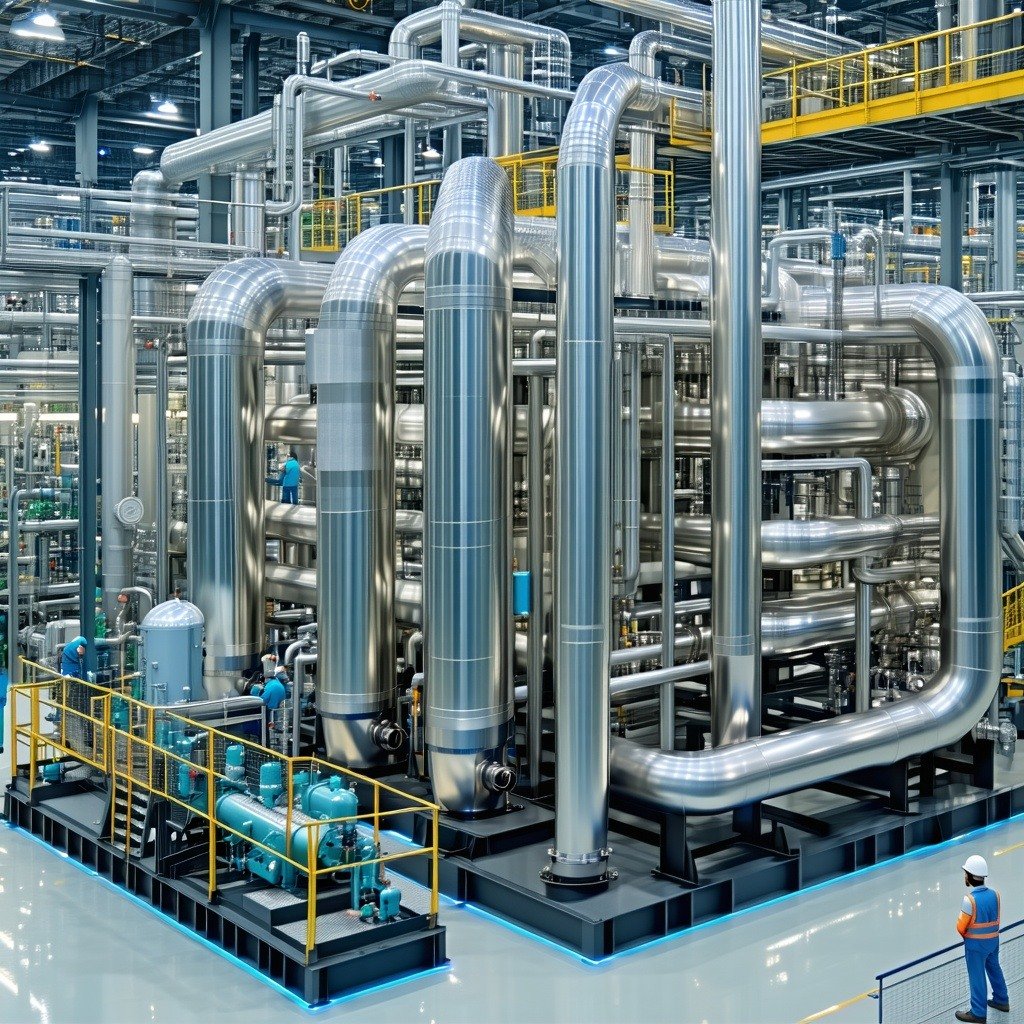
You don’t need to be a thermal engineer to appreciate what a heat exchanger does – but if you’re running industrial systems, cooling high-performance equipment, or producing energy, you definitely need to understand what the right one can do for you. This guide breaks down the most common heat exchanger applications across industries, explains how they work, and helps you figure out which type of exchanger fits your needs.
Heat Exchanger Types
When you’re deciding between different types of heat exchangers and their applications, the goal is simple: find the unit that meets your specific thermal demands, fits your space, and won’t be a nightmare to maintain. Each type offers different strengths.
- Gasketed Plate Heat Exchangers (GPHEs): These modular units are built for flexibility and maintainability. You can open them up, clean the plates, replace gaskets, and scale the system as your needs change. Ideal for industries where uptime is crucial but fouling is a risk—like chemical, marine, and HVAC.
- Welded Block Heat Exchanger: This fully welded, compact unit handles aggressive fluids and high temperatures without the need for gaskets. It’s perfect when you need a durable, low-maintenance option in extreme environments like petrochemicals, offshore platforms, or demanding process industries.
- Shell and Plate Heat Exchanger: A hybrid of traditional shell-and-tube and plate designs, these units deliver high pressure and thermal efficiency in a smaller footprint. They're used where compactness and reliability are non-negotiable.
- Shell and Tube: These beasts handle high pressure and temperature. You’ll find them in power plants, refineries, and chemical processing – anywhere rugged reliability is non-negotiable.
There are many different types of heat exchangers and their applications vary widely – from mission-critical process cooling to small-scale thermal recovery. Understanding heat exchanger types and applications ensures you avoid costly mismatches.
Refrigeration
The role of the heat exchanger in refrigeration is straightforward: absorb heat from one medium and release it somewhere else. Without a solid refrigeration heat exchanger, you’re dealing with inefficiencies, breakdowns, and spoiled product. The design and selection of a refrigerant heat exchanger can make or break performance in cooling systems.
Sub-applications:
- Commercial refrigeration: Grocery stores, cold display units, walk-ins – they all rely on refrigerant heat exchangers to keep food safe and fresh.
- Industrial refrigeration: Think food processing plants and cold storage logistics hubs – where durability and efficiency are vital.
- HVAC systems: In buildings, heat exchangers support reliable, energy-efficient air conditioning and climate control.
In these systems, refrigerant heat exchangers are responsible for transferring energy from the cooled environment into the refrigerant, which then circulates through compressors and condensers to release that heat elsewhere. The efficiency of this process hinges on low pressure drop, high heat transfer surface area, and material compatibility with refrigerants.
Compact plate heat exchangers, especially brazed or gasketed types, offer minimal footprint and quick thermal response, making them ideal for temperature-sensitive applications. A heat exchanger in refrigeration applications has to maintain thermal balance while minimizing energy loss – especially under fluctuating loads.
Tranter insight:
Tranter supports refrigeration with shell and plate heat exchangers, engineered for high efficiency and safety, especially when working with ammonia or mixed hydrocarbon refrigerants. Their robust performance and reliability make them a solid fit for industrial-scale cooling systems.
Power Generation
In any power generation setup – whether you’re working with coal, gas, or nuclear – heat exchangers are at the heart of thermal management. A heat exchanger in a power plant ensures that energy conversion is maximized and downtime minimized. Each type of generation has unique demands.
Sub-applications:
- Heat exchanger in steam power plant environments: Manages the temperature and pressure of the steam cycle, condensing exhaust steam back into water for reuse.
- Gas and coal-fired power: Heat exchangers play a role in flue gas heat recovery, preheating feedwater, and cooling auxiliary systems.
- Nuclear power heat exchanger applications: These are mission-critical components that transfer heat from radioactive coolant to secondary loops, often using leak-proof or double-walled designs.
A heat exchanger in power generation needs to deal with high pressures, fluctuating loads, and thermal stress. For steam power plants, it helps regulate the steam cycle for turbine performance. In gas-fired plants, it recovers exhaust heat for better fuel efficiency. In nuclear facilities, where safety is paramount, nuclear power heat exchanger systems isolate radioactive fluids while maintaining peak thermal transfer. Materials used must resist scaling, corrosion, and thermal fatigue to withstand years of operation.
Tranter insight:
For power generation, Tranter offers gasketed and welded plate heat exchangers designed for steam cycle optimization, lube oil cooling, and heat recovery across turbines, transformers, and generators. These exchangers are built to handle high stress and deliver consistent performance – exactly what’s needed from a heat exchanger in a power plant environment.
Heating and Cooling
Thermal management is everywhere. Whether you're running a district energy system or just trying to prevent a server farm meltdown, the right thermal heat exchanger keeps things in check. Heat exchangers for heating and cooling are tailored to deliver precise energy transfer across diverse applications.
Common Use Cases:
- District heating: Heat exchangers transfer thermal energy from a central plant to individual buildings, maximizing system efficiency and reducing loss.
- Process cooling: Used in industrial settings to keep equipment from overheating, particularly in high-speed or continuous manufacturing environments.
- Data centers: These rely heavily on cooling heat exchangers to regulate air or liquid temperatures and prevent downtime.
- Greenhouse and HVAC systems: Balance climate conditions to boost yield or comfort without excessive energy consumption.
A heat exchanger for heating uses a hot medium like water or steam to transfer energy into a secondary loop – often through a compact plate design that allows high surface contact. A heat exchanger for cooling does the opposite, pulling heat from systems or air and transferring it to water, glycol, or air. These cooling heat exchanger systems need to react quickly and maintain stability under continuous demand. In both cases, the thermal heat exchanger is the unsung hero of energy efficiency and process control.
Tranter insight:
Tranter provides gasketed plate and frame heat exchangers specifically for energy, heating, and cooling applications. These exchangers help balance energy demand and reduce system losses across HVAC networks, data centers, and municipal heating systems.
Chemical Processing
The chemical industry pushes heat exchangers to the limit. You’re dealing with corrosive fluids, aggressive reactions, and tight tolerances. The right chemical heat exchanger doesn’t just handle heat – it helps you control the entire process and safeguard your chemical processing equipment.
Sub-applications:
- Fluid-to-fluid transfer: Heat exchangers stabilize reaction temperatures between solvents, reactants, or intermediates.
- Gas-to-gas processes: Essential in capturing and reusing heat from exhaust streams or process gas conditioning.
- Handling corrosive media: Common in acid production, polymer manufacturing, or any process with aggressive chemicals.
Chemical processing equipment must meet strict demands for cleanliness, thermal control, and reliability. A chemical heat exchanger in these settings needs to be resistant to fouling and corrosion. That’s where materials like titanium, Hastelloy, or stainless steel come in. Plate exchangers are widely used due to their compact size, serviceability, and ability to handle complex fluids. Gasketed plate models are especially useful when you need to clean, inspect, or modify the setup regularly.
Tranter insight:
Tranter’s plate and frame heat exchangers are optimized for large cooling duties in chemical plants, offering high surface area efficiency, close temperature approaches, and easy maintenance – all essential for consistent output and uptime in complex chemical environments.
Industrial Manufacturing
When it comes to applications of heat exchangers in industry, one size never fits all. You’ve got thousands of processes across sectors – each with its own heat transfer needs. The right system supports uptime, product quality, and energy recovery. Industrial heat exchanger types vary from compact units to massive systems designed for intense throughput.
Sub-applications:
- Heavy manufacturing: Heat exchangers are used to cool hydraulic oil, temper furnaces, and recover energy from hot gases.
- Consumer goods: Processes like injection molding, bottling, or baking depend on precise heating and cooling cycles.
- Textiles, automotive, pulp & paper: From drying paper to painting vehicles, industrial heat exchanger types play a silent but critical role.
Heat exchangers in manufacturing help stabilize systems, protect machinery, and reduce waste. In steel or glass production, for example, shell-and-tube models cool down exhaust gases and refractory walls. In consumer product lines, plate exchangers maintain consistent process temperatures to prevent variation or spoilage. Key features for these applications include resistance to clogging, scalability for production changes, and easy integration into existing setups.
Tranter insight:
Tranter delivers gasketed plate and frame heat exchangers for integration into industrial manufacturing and machinery systems – including diesel engines – to prevent overheating, optimize performance, and ensure long-term operational reliability.
You’ve seen what heat exchangers can do – and where they’re doing it. If you’re looking to upgrade your system, troubleshoot inefficiencies, or just learn what’s possible with today’s technology, don’t guess. Head over to our website and learn more about heat exchangers and their role in various applications.